|
Центральное конструкторское бюро
арматуростроения
(ЦКБА)
АРМАТУРА ТРУБОПРОВОДНАЯ. РАСЧЕТ ПОКАЗАТЕЛЕЙ НАДЕЖНОСТИ НА
ЭТАПЕ ПРОЕКТИРОВАНИЯ.
РД 24-207-06-90
Дата введения 01.07.91
УТВЕРЖДЕНО
Указанием Минтяжмаша СССР
№ АВ-002-1-8993 от 20.09.90
Дата введения 01.07.1991 г.
ЛИСТ УТВЕРЖДЕНИЯ
Первый заместитель начальника научно-технического отдела
Минтяжмаша
|
В.А. Мажукин
|
Начальник сектора
|
А.Н. Полтарецкий
|
Главный инженер ЦКБА
|
М.И. Власов
|
Заместитель директора по научной работе
|
Ю.И. Тарасьев
|
Начальник отдела 161
|
Р.И. Хасанов
|
Начальник лаборатории 151
|
Г.В. Котылевский
|
Ответственный исполнитель - инженер-конструктор I
категории
|
Т.Г. Потемкин
|
СОГЛАСОВАНО
Представитель
заказчика 953
______________М.С.
Байбурин
«31» августа 1990 г.
Настоящий
руководящий документ (РД) устанавливает методику оценки значений показателей
надежности (безотказности и долговечности) трубопроводной арматуры, ее узлов и
приводных устройств к ней (далее изделие) на этапе проектирования.
СОДЕРЖАНИЕ
1.1. В
руководящем документе принята терминология по ГОСТ
27.002. Обозначения, применяемые при расчетах, приведены в приложении 1.
1.2.
Оценка надежности изделия на этапе проектирования определяется расчетом и
основана на использовании опытных данных ЦКБА, а также данных технической
литературы о надежности элементов изделия.
1.3.
Результаты расчета должны использоваться для предварительной оценки надежности
изделия на этапе проектирования и сравнения возможных вариантов конструкции.
Полученные расчетные данные должны быть в дальнейшем уточнены и дополнены
результатами испытаний на надежность. Окончательный вывод о надежности
спроектированного изделия составляется путем сбора и анализа статистических
данных о работе изделия в условиях эксплуатации.
1.4.
Оценка надежности на этапе проектирования проводится с целью:
-
сравнения различных вариантов структурной и конструктивной схем изделия;
-
выявления деталей и узлов, комплектующих элементов, лимитирующих надежность
изделия;
-
проверки соответствия прогнозируемого уровня надежности требованиям
технического задания;
-
анализа возможности выполнения заданных требований по надежности.
1.5. За
количественный критерий безотказности изделия принимается вероятность
безотказной работы в течение заданного срока (периода непрерывной работы,
гарантийного срока, гарантийной наработки, назначенного ресурса) или наработка
на отказ.
1.6. За
количественный критерий долговечности принимается ресурс или срок службы
изделия по номенклатуре показателей надежности, приведенных в техническом
задании (ТЗ) в соответствии с РД 302-07-278-89.
1.7.
При составлении расчета должны быть оговорены все принимаемые допущения.
1.8.
Расчет показателей надежности выполняется в соответствии с настоящим РД. Метод
расчета выбирается исполнителем из изложенных в разделах 2 и 3 исходя из требований
ТЗ,
Если
изделие состоит из узлов и деталей, информация о надежности которых имеется, то
расчет безотказности рекомендуется производить 1 методом или 2 методом.
Если
информация о надежности узлов или деталей нового изделия отсутствует, или
требования к вероятности безотказной работы выше величины 0,997, то расчет
безотказности рекомендуется производить 3
методом. Допускается по согласованию с заказчиком определение показателей
безотказности относительно отдельных видов-отказов (2 методом.).
1.9.
Вероятность безотказной работы или λ-характеристики комплектующих изделий принимается по данным
предприятия-изготовителя комплектующего изделия.
1.10.
При отсутствии в приложении 2
данных о вероятности безотказной работы (интенсивности отказов) узлов и деталей
при расчётах пользоваться статистическими данными.
2. МЕТОДЫ ОЦЕНКИ ПОКАЗАТЕЛЕЙ БЕЗОТКАЗНОСТИ
2.1.1.
Основные допущения, принимаемые при расчете:
а)
отказы элементов являются событиями случайными и независимыми;
б)
вероятность безотказной работы элементов изделия определяется экспоненциальным
законом, если нет достаточного числа опытных данных, свидетельствующих о другом
законе распределения;
в) все
элементы одного и того же типа имеют одинаковую интенсивность отказов;
г)
интенсивность отказов принимается постоянной, то есть из рассмотрения исключаются
периоды приработки и износа.
При
составлении расчета должны быть оговорены и все другие принимаемые допущения,
возникшие в связи со спецификой изделия, условий эксплуатации.
2.1.2.
Исходными данными для расчета являются:
а)
техническое задание;
б) сборочный
чертеж изделия и спецификация;
в)
заданный период, в течение которого необходимо определить вероятность
безотказной работы арматуры (период непрерывной работы, назначенный ресурс,
гарантийная наработка, гарантийный срок и т.д.);
г)
время совершения одного цикла;
д)
режим работы изделия;
е)
интенсивности отказов или ВБР узлов и деталей изделия.
Время
совершения одного цикла и режим работы изделия необходимы для расчета времени
работы отдельных узлов и элементов изделия.
Необходимо
установить, является ли изделие нормально открытым или нормально закрытым и
какова продолжительность его пребывания в открытом (или закрытом) положении в
процентах от заданного периода.
2.1.3.
Методика расчета
2.1.3.1.
Расчет вероятности безотказной работы изделия производится, исходя из основной
количественной характеристики надежности λ0i, данные о которой для различных элементов и узлов приведены
в приложении 2.
2.1.3.2.
При расчете изделие условно разбивается на элементы (узлы) и составляется
логическая схема соединений элементов (узлов). Логические схемы соединения
элементов (узлов) и соответствующие им формы для расчета вероятности
безотказной работы изделия Рс по данным вероятности безотказной работы
элементов Рj
следующие;
а)
простая последовательная схема (резервирование отсутствует):


|
(1)
|
б)
простая параллельная схема с (K-I)
резервными элементами:


|
(2)
|
в)
последовательно-параллельная схема (резервирование последовательных схем):
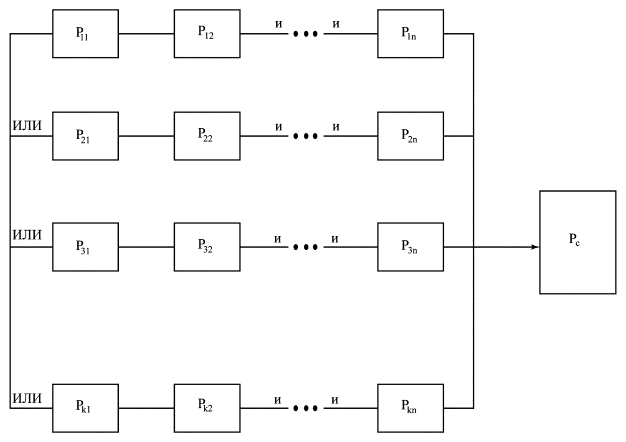
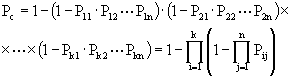
|
(3)
|
г)
параллельно-последовательная схема (поэлементные резервирования):
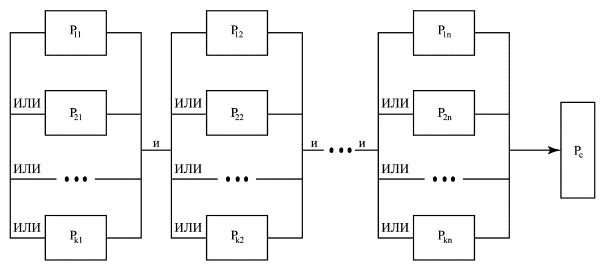

|
(4)
|
или,
если все Pij = Pj, то

|
(4а)
|
2.1.3.3.
Для каждого элемента необходимо определить:
а)
время t',
в течение которого элемент находится под нагрузкой;
б)
время t'', в течение которого элемент
находится в ненагруженном состоянии
Причем,

|
(5)
|
2.1.3.4.
Интенсивность отказов i-го
элемента, находящегося под нагрузкой, определяется по формуле;
в)
интенсивность отказов i-го элемента, не находящегося
под нагрузкой, определяется по формуле:

|
(7)
|
где а2-
|
поправочный
коэффициент, учитывающий уменьшение интенсивности отказов для ненагруженного элемента;
для
электрических элементов он выбирается по данным приложения
4; для остальных он равен 1·10-3
|
|
|
|
2.1.3.5.
Вероятность безотказной работы одного i-го элемента рассчитывается по
формуле (8), (9), (10).
а)
λ0i в единицах 1/час

|
(8)
|
б) λ0i в единицах 1/цикл

|
(9)
|
в)
вероятность безотказной работы i-элемента за фиксированный срок или наработку t*
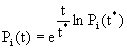
|
(10)
|
2.1.3.6. Вероятность безотказной работы j-ой
группы элементов Pj, объединенных по признаку равной продолжительности работы
при условии, что все элементы составляют последовательную схему, рассчитывается
по формулам:
а) если
Pi(t) рассчитывается по формуле (8), то
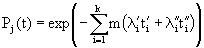
|
(11)
|
б) если
Pi(t) рассчитывается по формуле (9), то
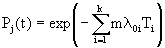
|
(12)
|
в) если
Pi(t) рассчитывается по формуле (10), то

|
(13)
|
2.1.3.7.
Вероятность безотказной работы всего изделия Pc определяется по формулам (1), (2),
(3), (4)
в зависимости от схемы соединения элементов в изделии.
2.1.3.8.
Для расчета вероятности безотказной работы отдельных элементов необходимо
заполнить таблицу 1 приложения 5.
2.1.3.9.
Пример расчета показателей надежности данным методом приведен в приложении 2.
2.2.1.
Основные допущения, принимаемые при расчете:
а)
отказы элементов являются событиями случайными и независимыми; ,
б)
вероятность безотказной работы элементов изделия определяется экспоненциальным
законом, если нет достаточного числа опытных данных, свидетельствующих о другом
законе распределения;
в) все
элементы одного и того же типа имеют одинаковую интенсивность отказов.
2.2.2.
Исходными данными для расчета являются:
а)
техническое задание;
б)
сборочный чертеж изделия и спецификация;
в)
критерии отказов и предельных состояний изделия;
г)
заданный период, в течение которого необходимо определить вероятность
безотказной работы изделия (период непрерывной работы, назначенный ресурс,
гарантийный срок и т.д.);
д)
интенсивности отказов узлов и деталей изделия.
2.2.3.
Методика расчета
2.2.3.1.
Вероятность безотказной работы изделия в течение заданного периода t-P11(t) определяется по формуле
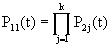
|
(14)
|
где P2j(t)-
|
вероятность
безотказной работы по каждому виду отказов;
|
k-
|
число
видов отказов или предельных состояний.
|
|
|
|
При
расчете вероятностей Р2j(t) учитываются только те узлы и
детали изделия, которые влияют на данный вид отказа.
2.2.3.2.
Для оценки вероятности безотказной работы изделия следует построить схему
следующим образом:
1
уровень - состояние изделия (работоспособное, неработоспособное) или событие
(отсутствие отказов);
2
уровень - события, состояния, функции, от которых зависит 1 уровень (критерии
отказов и продельных состояний);
3 (и
последующие) уровни - элементы изделия или события, от которых зависит 2
(предыдущий) уровень.
При
построении схемы необходима использовать следующие обозначения:

|
- состояние, событие, функция
(нет исходной информации);
|

|
- элементы (детали, узлы)
изделия (есть исходная информация - интенсивность отказов);
|

|
- "И" (знак:
зависимости);
|

|
- "не"
|

|
- "или"
|
По
схеме заполнить таблицу 2 приложения 5.
2.2.3.3.
Если события или элементы изделия связаны знаком "и", то вероятность
безотказной работы i-го уровня определяется по
формуле
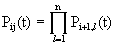
|
(15)
|
где n-
|
число
событий или элементов (i+1) уровня, влияющие на наступление события i-го
уровня.
|
|
|
|
Если
события или элементы изделия связаны знаком "или", то вероятность
безотказной работы определяется по формуле

|
(16)
|
2.2.3.4.
Вероятность безотказной работы в течение заданного периода t
определяется для каждого события, состояния, обозначенного на схеме прямоугольником.
Расчет
производится от нижнего уровня к верхнему.
Вероятность
безотказной работы элемента Pij в течение
заданного периода t
определять исходя из данных приложения 2, 3 и 4 по
формулам (8)-(10) или соответственно по формулам (11)-(13).
2.2.3.5.
Классификатор отказов и продельных состояний арматуры приведён в приложении 7.
2.2.3.6.
Пригар расчета по данному
методу приведен в приложении II.
2.3.1.
Основные допущения, применяемые при
расчете:
а)
отказы изделий являются случайными и независимыми
событиями
б) распределение
значений параметров работоспособности изделий и механических свойств конструкционных материалов подчиняются нормальному закону распределения
отказов,
2.3.2.
Исходными данными для расчета являются:
а)
техническая документация на изделие;
б)
критерии отказов и предельных
состояний;
в)
предельные значения параметров функционирования,
соответствующие критериям отказа и
предельных состояний;
г)
силовой и прочностной расчет изделия;
д)
справочные данные о коэффициентах вариации аналогичных выходных параметров
изделий - прототипов и механических свойств конструкционных материалов,
2.3.3.
Методика расчёта
2.3.3.1.
Вероятность безотказной работы изделия в течение заданного периода t
определяется по формуле

|
(17)
|
где P1(t)-
|
вероятность
неразрушения изделия в течение периода t ;
|
P2(t)-
|
вероятность невыхода параметров функционирования за
допустимые границы в точение заданного периода t.
|
|
|
|
2.3.3.2.
Расчет вероятности Р1(t).
Расчет
вероятности Р1(t) может быть определен двумя способами:
а)

|
(18)
|
где P1i(t)-
|
вероятность
неразрушения i-го
элемента или узла изделия в течение периода t ;
|
|
|
|
б)

|
(19)
|
Т.е. P1(t) определяется вероятность
неразрушения наиболее слабого узла или детали изделия в течение времени t. Наиболее
слабый элемент определяется по изделию прототипу или по прочностному расчету
(имеющий наименьший запас прочности или текучести).
Величина
P1i(t)
определяется по формуле
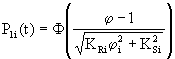
|
(20)
|
где φi-
|
коэффициент запаса, определяемый по формуле
|

|
(21)
|
где MRi и MSi-
|
ожидаемые
средние значения прочности R и нагрузки S;
|
KRi , KSi-
|
коэффициенты
вариации MRi и MSi соответственно.
|
|
|
|
|
Для
расчета величин P1i
заполняется таблица 1 приложения 6.
По
результатам силового и прочностного расчета заполняются графы 1-4 (см.сводную
таблицу напряжений).
В графе
5 определяется коэффициент запаса прочности 
В графу
6 вносятся значения коэффициент вариации прочности, определяемый по таблице приложения 8 исходя
из материала изготовления детали.
В графу
7 вносят значения коэффициента вариации нагрузки KSi. Если нет данных о его
величине, то значения KSi выбираются из интервала [0,2÷0,3]
В графе
8 определяют значения P1i(t). Значения
функции нормального распределения Ф(x) определяют по таблице приложения 9
в зависимости от x.
2.3.3.4.
Расчет вероятности P2(t).
Вероятность
невыхода параметров функционирования за допустимые границы в течение периода t
определяется по формулам:
a)
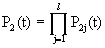
|
(22)
|
где P2j(t)-
|
вероятность
невыхода значений j-го
параметра функционирования за допустимые
пределы в течение периода t.
|
|
|
|
б)

|
(23)
|
т.е. P2(t) определяется вероятностью
невыхода за допустимые пределы наиболее "слабого" параметра
функционирования изделия.
Величина
P2j(t)
определяется следующим образом:
- если
параметр функционирования ограничен сверху
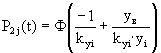
|
(24)
|
- если
параметр функционирования ограничен снизу

|
(25)
|
- если
паpaметр
функционирования имеет двухстороннее ограничение
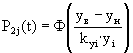
|
(26)
|
где Ф(…)-
|
функция
нормального распределения, определяемая по приложению
9;
|
yв, yн-
|
соответственно
верхняя и нижняя допустимые границы значений параметра, заданных в ТЗ;
|
yi-
|
ожидаемое
среднее значение параметра, определяется по результатам технических расчетов
или задается;
|
kyi-
|
коэффициент
вариации параметра работоспособности, определяемой по приложению 8.
|
|
|
|
Для
расчета значений P2j заполняют таблицу
2 приложения 6.
В графу
1 вносят параметры функционирования изделия.
В графу
2 - средние значения, параметра yi задаваемые ориентировочно по
данным конструкторского отдела.
В графу
3 вносят величину, ограничивающую
значения параметра функционирования.
Принимается по нормативным документам
(ГОСТ
9544-75, ОСТ 26-07-1375-82, ОТТ-87
и др.) или задается заказчиком в техническом задании.
В графу
4 вносят значения коэффициента вариации
параметра функционирования kyi;
Величина
kyi определяется по таблице
приложения 8.
В графа
5 определяют значения аргумента uj функции нормального распределения Ф(uj).
В графе
6 определяют значения вероятности P2j по формулам (24)-(26). Значения функции Ф(uj) определяют по приложению
9 в зависимости от uj.
Примечание.
При испытаниях опытных образцов или макетов величину yi следует
контролировать и в случае отклонения от принятой в расчете, расчет
откорректировать.
2.4. Оценка наработки на отказ
2.4.1.
Наработка на отказ изделия определяется по формуле

|
(27)
|
где i={1,r}-
|
число узлов и деталей
изделия, лимитирующих наработку на отказ;
|
Ti-
|
наработка на отказ или ресурс i-го узла (детали).
|
|
|
|
2.4.2.
Значения Тi определяются по формуле

|
(28)
|
где λi-
|
интенсивность отказов i-го узла или детали,
определяется по приложению
2.
|
|
|
|
При
определении наработки на отказ в циклах при расчете принимать λi в
единицах 1/цикл, при определении наработки на отказ в часах - в единицах 1/час,
2.4.3.
Допускается определение Ti по формулам, приведенным в
нормативно-технической документации на узлы и детали.
3. МЕТОДЫ ОЦЕНКИ
ПОКАЗАТЕЛЕЙ ДОЛГОВЕЧНОСТИ
3.1.1.
Полный средний срок службы изделия Tсл.ср.
определяется по формуле

|
(29)
|
где Tj-
|
срок службы корпусных деталей и узлов, не подлежащих
замене и ремонту, определяющих долговечность изделия.
|
|
|
|
3.1.2. Величина
Tj определяется по формуле (30) или (31)

|
(30)
|
где λj-
|
интенсивность отказов i-го
узла или детали,
лимитирующих долговечность изделия.
|
|
|
|
Величина
λj
определяется по приложению 2
в единицах измерения 1/час

|
(31)
|
где γj-
|
скорость изнашивания или скорость коррозии детали или
узла.
|
Umax-
|
максимально допустимый износ.
|
|
|
|
Скорость
коррозии и скорость изнашивания определяются расчетным путем исходя из
коэффициентов износостойкости и коррозионной стойкости применяемых материалов.
Величина
коэффициента износостойкости определяется расчетно-экспериментальными методами
либо по таблицам приложения
10.
Величина
Umax определяется расчетным путем исходя из запаса прочности, и приводится в технической
документации.
Примечание: Допускается
определение Tj по формулам нормативно-технической документации на узлы и детали, лимитирующие
долговечность арматуры или по результатам прочностного расчета.
3.1.3.
Полный назначенный срок службы Tсл н
определяется по формуле

|
(32)
|
где n-
|
коэффициент запаса по сроку службы;
|
Tсл ср-
|
полный средний срок службы изделия, определяемый по
формуле (29).
|
|
|
|
Величина
n выбирается
в зависимости от критичности (значимости последствий) отказа из ряда
[2÷13] и согласовывается с заказчиком при необходимости»
3.2.1.
Полный средний рзеурс изделия Тр ср определяется по формуле
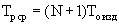
|
(33)
|
где N-
|
число ремонтов арматуры;
|
То изд-
|
наработка на отказ, определяемая по п.2.4.
|
|
|
|
Величина
Tо изд при определении ресурса
регулирующей арматуры должна измеряться, в часах, для остальной арматуры - в
циклах.
3.2.2.
Полный назначенный ресурс Трн определяется по формуле

|
(34)
|
где m-
|
коэффициент запаса по ресурсу.
|
|
|
|
Величина
m
выбирается в зависимости от критичности отказов из ряда [2÷13] и при
необходимости согласовывается с заказчиком.
4. ТРЕБОВАНИЯ К ОФОРМЛЕНИЮ РАСЧЕТА
4.1.
Расчет надежности на этапе проектирования следует оформлять в соответствии с
требованиями ГОСТ 2.105-79.
4.2.
Расчет должен содержать следующие разделы:
-
задача. расчета;
-
основные допущения, принимаемые при расчете;
-
исходные данные;
-
расчет показателей надежности;
-
выводы (заключение).
4.3. В
разделе "Выводы" полученное расчетом значение показателя надежности-Up
следует сравнить со значением, заданным в техническом задании Uтз
Приложение 1(Справочное). Обозначения,
применяемые при расчетах:
|
I Метод
|
t-
|
период непрерывной работы, гарантийный срок, гарантийная наработка, назначенный ресурс (час, цикл);
|
t'-
|
время,
в течение которого элемент в составе эксплуатируемого
изделия находятся под
нагрузкой, сказывающейся решающим образом
на его надежности (час);
|
t''-
|
время,
в течение
которого элемент в составе эксплуатируемого
изделия находится в
ненагруженном состоянии, не сказывающимся
решающим образом на его надежности, или остается ненагруженным (час);
|
tц-
|
время совершения одного цикла
(час);
|
λ0i-
|
интенсивность отказов i-го элемента (узла) (1/час, 1/цикл)
|
λ'i-
|
интенсивность
отказов i-го элемента (узла), находящегося под
нагрузкой в течение времени t' (1/час, 1/цикл);
|
λi''-
|
интенсивность
отказов i-го элемента (узла), ненагруженного
в течение времени t'' (I/час, 1/цикл);
|
P(t)-
|
вероятность безотказной работы
изделия в течение времени t;
|
Pi(t)-
|
вероятность безотказной работы i-го элемента (узла) в течение времени t;
|
Pj(t)-
|
вероятность безотказной работы j-ой
группы элементов;
|
m-
|
число типов элементов в изделии;
|
a1-
|
коэффициент, учитывающий
увеличение интенсивности отказов
нагруженных элементов;
|
а2-
|
поправочный коэффициент,
учитывающий уменьшение интенсивности отказов для ненагруженных элементов;
|
Т-
|
наработка арматуры в заданный
период (час, цикл)
|
|
II Метод
|
Р11(t)-
|
вероятность безотказной работы
изделия в течение заданного периода t ;
|
P2j(t)-
|
вероятность безотказной работы
по каждому виду отказов;
|
k-
|
число видов отказов или
предельных состояний;
|
Т-
|
число циклов срабатывания в
заданный период;
|
λij-
|
интенсивность отказов ( i j )
элемента изделия.
|
|
III
Метод.
|
Р(t)-
|
вероятность безотказной работы
изделия в течение заданного периода t ;
|
Р1(t)-
|
вероятность неразрушения
изделия в течение периода t ;
|
P2(t)-
|
вероятность невыхода
параметров работоспособности за допустимые границы в течение заданного
периода t
;
|
kyi-
|
коэффициент вариации параметра
работоспособности;
|
yi-
|
ожидаемое среднее значение
параметра работоспособности;
|
ун, yв-
|
соответственно нижняя и
верхняя допустимые границы значений параметра работоспособности yi;
|
MR, MS-
|
ожидаемые средние значения
прочности R
и нагрузки S;
|
KR, KS-
|
коэффициенты, вариации MR и MS соответственно;
|
φi-
|
коэффициент запаса прочности;
|
Ф(…)
|
Функция нормального
распределения.
|
|
Оценка наработки на отказ
|
Tо изд-
|
наработка на отказ изделия
(час, цикл);
|
Тi-
|
наработка на отказ или ресурс i-го узла
(детали), (час, цикл);
|
r-
|
число деталей и узлов,
лимитирующих наработку на отказ изделия;
|
λi-
|
интенсивность отказов i-го узла
или детали (1/час, 1/цикл);
|
|
Методы оценки показателей
долговечности
|
Tсл ср-
|
полный средний срок службы
изделия, (год, лет);
|
Tj-
|
срок службы корпусных деталей
и узлов, определяющих долговечность изделия (год, лет);
|
λj-
|
интенсивность отказов j-го узла
или детали, лимитирующих долговечность изделия (1/час, 1/цикл);
|
Umax-
|
максимально допустимый износ;
|
γj-
|
скорость изнашивания j-й детали
или узла (мм/год);
|
Tсл н-
|
полный назначенный срок службы
(год, лет);
|
n-
|
коэффициент запаса по сроку
службы;
|
Тр ср-
|
полный средний ресурс изделия
(час, цикл);
|
m-
|
коэффициент запаса по ресурсу
|
Tрн-
|
полный назначенный ресурс
изделия, (час, цикл);
|
N-
|
количество ремонтов изделия.
|
Приложение 2(Справочное). Показатели
надежности элементов арматуры
1.
Приложение 2 составлено на основе данных испытаний и эксплуатации арматуры и ее узлов, имеющихся в ЦКБА. Данные
сведены в таблицу, которая будет дополняться по мере появления новых данных.
2. В
таблице приведены три значения λо:
наибольшее, среднее и наименьшее. Наибольшее значение λo следует
принимать при тяжелых условиях работы изделия (Р - свыше 200 кгс/см2, tº -
свыше 100°С, среда - агрессивная, вибрация - выше нормы) и больших гарантийных сроках или при малом запасе прочности, (n≤2,0).
В случае легких условий работы изделия (Р - до 200 кгс/см2, tº - до 100°С, среда - агрессивная,
вибрация - нормальная) и небольших гарантийных сроках (или при большом запасе
прочности n≥3,5)
применяются наименьшие значения λo.
При отсутствии каких-либо специальных условий и при запасе прочности от 2,0 до
3,5 следует принимать среднее
значение λo.
3. Для
элементов и узлов, отмеченных знаком * значения характеристик и вероятность
безотказной работы брать из соответствующих стандартов на данный элемент или
узел.
Примечание.
При расчете показателей безотказности по видам отказов (II
метод) использовать λ-характеристики
для соединений, сопряжений и поверхностей трения. При расчете показателей
безотказности I
методом применять λ-характеристики
для отдельных деталей и узлов арматуры.
Задвижки
Наименование
элемента, узла задвижки
|
Вероятность безотказной работы
P(t*)
|
Данные эксплуатации
λoi·10-6 1/час
|
Данные испытаний ЦКБА
λoi·10-6 1/цикл
|
наименьшее
|
среднее
|
наибольшее
|
наименьшее
|
среднее
|
наибольшее
|
1
|
2
|
3
|
4
|
5
|
6
|
7
|
8
|
Бурт
|
|
0,032
|
0,072
|
0,145
|
|
|
|
Винт стопорный
|
P(10
лет)=0,9986
|
|
|
|
|
|
|
Втулка резьбовая
|
P(10
лет)=0,9896
|
0,04
|
0,11
|
0,32
|
12,5
|
12,7
|
13,2
|
Гайка
|
P(10
лет)=0,999
|
|
|
|
|
|
|
Грибок
|
|
0,023
|
0,096
|
0,206
|
|
|
|
Диск
|
|
0,29
|
0,82
|
1,58
|
|
|
|
Клин
|
|
|
|
|
|
|
|
Цельный
|
|
0,52
|
0,82
|
1,41
|
|
|
|
Упругий
|
|
0,15
|
0,44
|
0,96
|
|
|
|
Составной
|
|
0,19
|
0,97
|
1,18
|
|
|
|
Корпус
|
|
|
|
|
|
|
|
Сталь
|
P(10
лет)=0,9995
|
|
|
|
|
|
|
чугун
|
P(10
лет)=0,999
|
|
|
|
|
|
|
Цветные сплавы
|
P(7
лет)=0,9992
|
|
|
|
|
|
|
Крышка
|
|
|
|
|
|
|
|
Сталь
|
P(10
лет)=0,9995
|
|
|
|
|
|
|
чугун
|
P(10
лет)=0,999
|
|
|
|
|
|
|
цветные сплавы
|
P(7
лет)=0,9992
|
|
|
|
|
|
|
Крепежные детали
|
P(10
лет)=0,9991
|
|
|
|
|
|
|
Направляющие, клина, корпуса
|
P(10
лет)=0,987
|
|
|
|
|
|
|
Сталь
|
|
0,009
|
0,024
|
0,142
|
|
|
|
Чугун
|
|
0,018
|
0,068
|
0,201
|
|
|
|
Ось
|
|
0,022
|
0,067
|
0,153
|
|
|
|
Прокладка уплотнительная
фторопластовая, металлическая
|
|
0,14
|
0,20
|
0,38
|
|
|
|
Паронитовая
|
|
0,09
|
0,28
|
0,52
|
|
|
|
Асбестовая
|
|
0,21
|
0,36
|
0,48
|
|
|
|
Поверхность трения
|
|
0,051
|
0,072
|
0,135
|
|
|
|
Рукоятка (маховик)
|
P(10
лет)=0,9992
|
|
|
|
|
|
|
Сальниковый узел с набивкой
|
|
|
|
|
|
|
|
фторопластовой
|
|
0,012
|
0,054
|
0,092
|
|
3,16
|
|
ФУМ
|
|
0,032
|
0,089
|
0,146
|
|
5,01
|
|
Асбестовой
|
|
0,061
|
0,174
|
0,238
|
|
6,24
|
|
Соединение крепежное
|
P(10
лет)=0,999
|
|
|
|
|
|
|
Резьбовое
|
P(10
лет)=0,988
|
|
|
|
|
|
|
Сварное
|
P(10
лет)=0,998
|
|
|
|
|
|
|
механическое кулачковое
|
P(10
лет)=0,998
|
0,093
|
0,240
|
1,291
|
|
|
|
Уплотнительные кольца корпуса, клина,
дисков, шибера:
|
|
|
|
|
|
|
|
твердый сплав
|
|
0,24
|
0,84
|
1,69
|
|
|
|
Сталь
|
|
0,18
|
0,88
|
1,82
|
|
|
|
цветные сплавы
|
|
0,02
|
0,92
|
1,96
|
|
|
|
Фланец
|
P(10
лет)=0,999
|
|
|
|
|
|
|
Шайба
|
P(10
лет)=0,997
|
|
|
|
|
|
|
Шибер
|
|
0,47
|
0,61
|
0,85
|
|
|
|
Шпиндель
|
|
0,07
|
0,095
|
0,18
|
|
|
|
Шпонка
|
P(10
лет)=0,996
|
|
|
|
|
|
|
Шпилька
|
P(10
лет)=0,998
|
|
|
|
|
|
|
Шарнирное
соединение
|
|
0,16
|
0,40
|
1,08
|
|
|
|
Шестерня
|
|
0,24
|
0,89
|
1,995
|
|
|
|
Клапаны с электромагнитным приводом
Наименование
элементов и узлов арматуры
|
Вероятность безотказной работы в
течении t*
P(t*)
|
Данные эксплуатации
|
Данные испытаний
|
λoi·10-6 1/час
|
λoi·10-6 1/цикл
|
наименьшее
|
среднее
|
наибольшее
|
наименьшее
|
среднее
|
наибольшее
|
1
|
2
|
3
|
4
|
5
|
6
|
7
|
8
|
Винт (стяжной)
|
|
0,07
|
1,02
|
2,96
|
|
|
|
Втулка
|
|
0,12
|
0,50
|
1,49
|
|
|
|
Диск
|
|
0,10
|
0,60
|
0,90
|
|
|
|
Зажим (клемма) -
|
|
0,003
|
0,004
|
0,005
|
|
|
|
Катушка электромагнитного привода
|
|
0,004
|
0,014
|
0,098
|
|
|
|
Клапанно-запорное устройство
(плавная посадка)
|
|
0,05
|
0,13
|
0,46
|
13,6
|
15,8
|
16,2
|
Клапанно-запорное устройство
(резкая посадка)
|
|
0,03
|
0,15
|
0,39
|
4,3
|
4,5
|
6,2
|
Клапан резинометаллический
(РМК)
|
|
0,04
|
0,12
|
0,21
|
3,4
|
5,1
|
6,4
|
Кожух
|
0,999 (10 лет)
|
0,09
|
0,6
|
1,4
|
|
|
|
Корпус:
|
|
|
|
|
|
|
|
Стальной
|
0,9995 (10 лет)
|
|
|
|
|
|
|
чугунный
|
0,999 (10 лет)
|
|
|
|
|
|
|
латунный
|
0,999 (7 лет)
|
|
|
|
|
|
|
пластмассовый
|
0,992 (5 лет)
|
|
|
|
|
|
|
Крышка:
|
|
|
|
|
|
|
|
Стальная
|
0,9995 (10 лет)
|
|
|
|
|
|
|
Чугунная
|
0,999 (10 лет)
|
|
|
|
|
|
|
Латунная
|
0,999 (7 лет)
|
|
|
|
|
|
|
Крепежные детали
|
0,999 (10 лет)
|
|
|
|
|
|
|
Кулачок (кулачковое соединение)
|
|
0,04
|
0,95
|
2,85
|
|
|
|
Манжета фторопластовая
|
|
0,070
|
0,093
|
0,210
|
|
|
|
Мембрана
резиновая
|
|
0,08
|
0,097
|
0,19
|
10,8
|
11,2
|
11,7
|
Мембрана фторопластовая
|
|
0,055
|
0,082
|
0,16
|
|
|
|
Муфта
соединительная
|
|
0,061
|
0,11
|
0,25
|
11,3
|
12,0
|
13,5
|
Поверхность трения .
|
|
0,06
|
0,072
|
0,14
|
7,1
|
7,4
|
8,6
|
Пробка резьбовая
|
|
0,003
|
0,017
|
0,183
|
15,0
|
16,8
|
18,9
|
Прокладка
резиновая
|
P(5
лет)=0,998
|
0,003
|
0,018
|
0,13
|
|
|
|
Прокладка фторопластовая
.
|
P(10 лет)=0,9974
|
0,0069
|
0,0096
|
0,0203
|
|
|
|
Прокладка
уплотнительная
(асбест, ФУМ, паронит)
|
P(10
лет)=0,998
|
0,0032
|
0,0056
|
0,0092
|
|
|
|
Пружина возвратная
|
0,9999 (10 лет)
|
0,007
|
0,014
|
0,40
|
|
|
|
Рычаг
|
0,997 (10 лет)
|
|
|
|
|
|
|
Ручной дублер ЭМП
|
0,99995(10 лет)
|
|
|
|
|
|
|
Сальниковый узел с набивкой:
|
|
|
|
|
|
|
|
Фторопласт
4
|
P(t*) по ОСТ 26-07-1232-87
|
0,009
|
0,012
|
0,015
|
|
|
|
ФУМ
|
0,010
|
0,014
|
0,019
|
|
|
|
Асбестотехнической
|
0,007
|
0,011
|
0,018
|
|
|
|
Сетка (фильтр)
|
|
0,09
|
0,20
|
0,63
|
|
|
|
Сильфон*
|
по ГОСТ 21744-83 или ОСТ 26-07-2019-81
|
|
|
|
Стойка
|
|
0,001
|
0,009
|
0,019
|
|
|
|
Соединение подвижное
|
|
0,014
|
0,052
|
0,102
|
|
|
|
Соединение сварное
|
0,999(10 лет)
|
0,009
|
0,056
|
0,097
|
6,49
|
6,51
|
6,69
|
Соединение жесткое
|
|
0,013
|
0,075
|
0,145
|
8,7
|
8,9
|
9,8
|
Соединение резьбовое
|
|
0,02
|
0,11
|
2,60
|
12,4
|
12,8
|
13,4
|
Соединение механическое
|
|
0,002
|
0,086
|
0,326
|
|
|
|
Толкатель
|
|
0,001
|
0,012
|
0,124
|
|
|
|
Трубка разделительная
|
|
0,011
|
0,077
|
0,145
|
|
|
|
Уплотнение скользящее
|
|
0,14
|
0,22
|
0,86
|
|
|
|
Уплотнение неподвижное
(резиновое)
|
|
0,51
|
0,73
|
4,2
|
|
|
|
Уплотнение ввода кабеля
|
P(10
лет)=0,999
|
|
|
|
|
|
|
Шайба
|
0,9995(10 лет)
|
|
|
|
|
|
|
Шпилька
|
|
0,007
|
0,018
|
0,072
|
15,0
|
16,2
|
18,0
|
Штифт
|
0,9995(10 лет)
|
0,007
|
0,017
|
0,064
|
15,0
|
16,0
|
17,8
|
Штуцер
|
|
0,001
|
0,009
|
0,051
|
|
|
|
Шток
|
|
0,043
|
0,067
|
0,079
|
7,95
|
8,0
|
8,4
|
Электромагнит
|
P(10
лет)=0,999
|
0,009
|
0,017
|
0,025
|
9,2
|
9,24
|
9,8
|
Клапаны запорные
Наименование
элементов и узлов арматуры
|
Вероятность безотказной работы в
течение t*
P(t*)
|
Данные эксплуатации
|
Данные испытаний
|
λoi·10-6 1/цикл
|
λoi·10-6 1/час
|
наименьшее
|
среднее
|
наибольшее
|
наименьшее
|
среднее
|
наибольшее
|
1
|
2
|
3
|
4
|
5
|
6
|
7
|
8
|
Бугельный узел без подшипников
|
P(t*)
по
ОСТ 26-07-2007-78
|
3,02
|
4,53
|
5,85
|
0,014
|
0,026
|
0,042
|
Бугельный узел
с подшипниками качения
|
P(t*)
по
ОСТ 26-07-2017-79
|
9,62
|
11,34
|
14,81
|
0,065
|
0,084
|
0,122
|
Винтовая пара
|
P(10
лет)=0,9992
|
|
|
|
0,012
|
0,030
|
0,059
|
Втулка
|
P(10
лет)=0,9995
|
|
|
|
0,010
|
0,018
|
0,027
|
Втулка резьбовая
|
P(10
лет)=0,997
|
9,86
|
12,92
|
14,86
|
0,072
|
0,113
|
0,281
|
Корпус
|
|
|
|
|
|
|
|
Стальной
|
P(10
лет)=0,9995
|
|
|
|
|
|
|
Чугунный
|
P(10
лет)=0,999
|
|
|
|
|
|
|
Титановый
|
P(10
лет)=0,999
|
|
|
|
|
|
|
Из цветных металлов
|
P(10 лет)=0,9983
|
|
|
|
|
|
|
Крепежные детали
|
P(10
лет)=0,9992
|
|
|
|
|
|
|
Крышка
|
P(10
лет):
|
|
|
|
|
|
|
Стальная
|
=0,9995
|
|
|
|
|
|
|
Чугунная
|
=0,999
|
|
|
|
|
|
|
Титановая
|
=0,999
|
|
|
|
|
|
|
Кулачок, кулачковое соединение
|
|
|
|
|
0,001
|
0,002
|
0,004
|
Маховик и рукоятка
|
P(10
лет)=0,9999
|
|
|
|
|
|
|
Манжета
|
|
|
|
|
0,04
|
0,06
|
1,10
|
Муфта
|
P(10
лет)=0,9994
|
|
|
|
|
|
|
Ось
|
P(10
лет)=0,999
|
|
|
|
|
|
|
Пара
трения ("шток-втулка", "втулка-стойка",
"корпус-золотник", "клин-корпус")
|
P(3000)=0,999
|
0,73
|
1,12
|
2,02
|
0,013
|
0,021
|
0,038
|
Поверхность трения
|
|
|
|
|
0,031
|
0,052
|
0,098
|
Подпятник
|
|
0,63
|
0,98
|
1,72
|
0,013
|
0,021
|
|
Подшипник качения
|
|
|
|
1,02
|
0,32
|
0,08
|
|
Подшипник скольжения
|
|
|
|
0,38
|
0,21
|
0,09
|
|
Пробка
|
|
|
|
|
|
|
|
Прокладка уплотнительная
фторопластовая
|
P(10
лет)=0,9974
|
|
|
|
0,0069
|
0,0097
|
0,0203
|
ФУМа
|
P(10
лет)=0,9974
|
|
|
|
0,0081
|
0,0092
|
0,0165
|
резиновая
|
P(5
лет)=0,998
|
|
|
|
0,0058
|
0,0152
|
0,0403
|
Пружина
|
P(10
лет)=P(1500ц)=0,9995
|
|
|
|
0,0006
|
0,0019
|
0,010
|
винтовая
|
P(10
лет)=0,9995
|
|
|
|
0,0006
|
0,0019
|
0,010
|
Возвратная
|
P(10
лет)=P(1500ц)=0,9996
|
|
|
|
|
|
|
невозвратная
|
P(10
лет) =0,9994
|
|
|
|
|
|
|
Тарельчатая
(на 1 тарелку)
|
P(10
лет)=P(1500ц)=0,9999
|
|
|
|
|
|
|
Пята
|
|
0,63
|
0,98
|
1,72
|
0,013
|
0,021
|
0,038
|
Резьбовая
ходовая пара
|
P(t*)
по
ОСТ 26-07-1232-87
P(10
лет)=0,999
|
|
|
|
0,007
|
0,026
|
0,059
|
Резьбовое
соединение
|
|
|
|
|
0,11
|
0,02
|
1,95
|
Сальниковый узел с
набивкой:
|
P(t*)
по
ОСТ 26-07-2050-82
|
|
|
|
|
|
|
Фторопласт 4
|
P(10
лет)=0,9992
|
|
|
|
0,009
|
0,014
|
0,017
|
ФУМ
|
|
|
|
0,010
|
0,014
|
0,019
|
Асбестотехнической
|
|
|
|
0,007
|
0,012
|
0,024
|
Сильфон
|
P(
t*
) по ГОСТ 21744-83 или ОСТ 26-07-2019-81
|
|
|
|
|
|
|
Соединение
|
|
|
|
|
|
|
|
резьбовое
|
P(10
лет)=0,998
|
|
|
|
0,011
|
0,020
|
1,95
|
Сварное
|
|
|
|
0,011
|
0,025
|
0,104
|
Кулачковое
|
|
|
|
0,032
|
0,076
|
0,121
|
Механическое
|
|
|
|
0,002
|
0,004
|
1,05
|
Шарнирное
|
|
|
|
0,952
|
0,627
|
0,432
|
Основного
разъема.
|
P(10
лет)=0,999
|
|
|
|
0,022
|
0,062
|
0,210
|
Стопор
|
P(10
лет)=0,9996
|
|
|
|
|
|
|
Наименование
элементов и узлов арматуры
|
P(t*)
|
Данные эксплуатации
|
Данные испытаний
|
λoi·10-6 1/цикл
|
λoi·10-6 1/час
|
наименьшее
|
среднее
|
наибольшее
|
наименьшее
|
среднее
|
наибольшее
|
1
|
2
|
3
|
4
|
5
|
6
|
7
|
8
|
Узел затвора с уплотнением металл по
металлу
|
|
|
|
|
|
|
|
Тип I, II
|
P(12
лет)=0,9994
|
|
|
|
|
|
|
(по ОСТ 26-07-2042-81)
|
P(3000ц)=0,992
|
8,2
|
10,6
|
16,8
|
0,0096
|
0,034
|
0,086
|
Тип III
|
P(1500ц)=0,993
|
10,3
|
15,7
|
19,7
|
|
|
|
Узел затвора с уплотнением из
фторопласта 4
|
|
|
|
|
|
|
|
Тип I-IV,VI (по ОСТ 26-07-1375-82)
|
P(3000ц)=0,999
P(12 лет)=0,9996
|
1,02
|
1,81
|
2,71
|
0,007
|
0,013
|
0,036
|
Тип V
|
P(3000ц)=0,99
|
4,49
|
7,24
|
10,65
|
|
|
|
Уплотнение - скользящее
|
|
|
|
|
0,011
|
0,027
|
0,084
|
Неподвижное (резиновое кольцо)
|
|
|
|
|
0,006
|
0,0152
|
0,043
|
Уплотнительная прокладка
(см.прокладка)
|
|
|
|
|
|
|
|
Узел крепления рукоятки и маховика
|
P(10
лет)=0,9995
|
1,51
|
2,01
|
2,89
|
|
|
|
Фланец
|
P(10
лет)=0,9995
|
|
|
|
|
|
|
Цилиндр
|
P(10
лет)=0,999
|
|
|
|
|
|
|
Шплинт
|
P(10
лет)=0,9992
|
|
|
|
|
|
|
Шпиндель
|
P( ) по ОСТ 26-07-1232-87
|
|
|
|
0,007
|
0,026
|
0,059
|
Шпоночное соединение
|
P(10
лет)=0,9994
|
|
|
|
|
|
|
Штифт
|
P(10
лет)=0,9992
|
|
|
|
|
|
|
Шток
|
P(12
лет)=0,998
|
0,73
|
1,12
|
2,02
|
0,013
|
0,021
|
0,038
|
Штуцер
|
P(10
лет)=0,9994
|
|
|
|
|
|
|
Краны
Наименование
элемента, узла арматуры
|
Вероятность безотказной работы в
течении t*
P(t*)
|
Данные эксплуатации
|
Данные испытаний ЦКБА
|
λoi·10-6 1/час
|
λoi·10-6 1/цикл
|
наименьшее
|
среднее
|
наибольшее
|
наименьшее
|
среднее
|
наибольшее
|
1
|
2
|
3
|
4
|
5
|
6
|
7
|
8
|
Гайка
накидная
|
P(10
лет)=0,999
|
|
|
|
|
|
|
Ключ
|
P(10
лет)=0,9992
|
|
|
|
|
|
|
Корпус
|
|
|
|
|
|
|
|
Латунный
|
P(10
лет)=0,992
|
|
|
|
|
|
|
Чугунный
|
P(10
лет)=0,992
|
|
|
|
|
|
|
Стальной
|
P(10
лет)=0,993
|
0,04
|
0,10
|
0,56
|
|
|
|
титановый сплав
|
P(10
лет)=0,992
|
|
|
|
|
|
|
Крепежные
детали
|
P(10
лет)=0,9988
|
|
|
|
|
|
|
Муфта
|
P(10
лет)=0,999
|
0,01
|
0,049
|
0,149
|
|
|
|
Пара
трения
|
|
|
|
|
|
|
|
"сальник-шток"
|
P(5
лет)=0,996
|
|
|
|
|
|
|
"клин-корпус"
|
P(2
года)=0,965
|
0,285
|
0,678
|
1,024
|
|
|
|
Ползун
|
|
0,010
|
0,132
|
0,423
|
|
|
|
Пробка
|
|
|
|
|
|
|
|
Латунная
|
|
0,04
|
0,99
|
1,26
|
2,41
|
3,75
|
4,45
|
Чугунная
|
|
0,45
|
1,02
|
1,36
|
|
|
|
Стальная
|
|
0,15
|
1,09
|
1,74
|
|
|
|
из титанового сплава
|
|
0,28
|
0,92
|
1,43
|
|
|
|
Прокладка
уплотнительная:
|
|
|
|
|
|
|
|
Фторопластовая
|
P(10
лет)=0,9974
|
|
|
|
|
|
|
Резиновая
|
P(8
лет)=0,9981
|
|
|
|
|
|
|
паронит, картон
|
P(8
лет)=0,9974
|
|
|
|
|
|
|
Ролик
|
P(10
лет)=0,9986
|
|
|
|
|
|
|
рукоятка
|
P(10
лет)=0,999
|
|
|
|
|
|
|
Сальниковый
узел
|
|
|
|
|
|
|
|
тип I, II, VI
|
P(t*) по
ОСТ
26-07-2030-81
|
|
|
|
|
|
|
ФУМ,
фторопласт
|
|
0,004
|
0,016
|
0,029
|
1,02
|
1,8
|
5,3
|
асбест,
паронит
|
P(10
лет)=0,9996
|
0,0009
|
0,0114
|
0,0236
|
0,08
|
1,8
|
4,6
|
Тип
III
фторопласт 4
|
P(
5000ц) =0,96
|
|
|
|
1,31
|
2,72
|
4,01
|
Тип
IV,V
резиновое кольцо
|
P(3000ц)=0,95
|
0,012
|
0,038
|
0,059
|
0,72
|
1,5
|
4,2
|
Соединение
|
|
|
|
|
|
|
|
Сварное
|
|
0,024
|
0,056
|
0,098
|
|
|
|
Резьбовое
|
|
0,01
|
0,11
|
0,35
|
11,2
|
12,5
|
12,65
|
Крепежное
|
|
0,004
|
0,017
|
0,059
|
|
|
|
Механическое
|
|
0,004
|
0,10
|
0,42
|
|
|
|
Уплотнительное
кольцо
|
|
0,32
|
0,73
|
1,04
|
|
|
|
Фторопластовое
|
|
|
|
|
|
|
|
Резиновое
|
|
0,11
|
0,51
|
0,94
|
|
|
|
Фланец
|
P(10 лет)=0,999
|
|
|
|
|
|
|
Шар
(пробка)
|
|
|
|
|
|
|
|
латунь, бронза
|
|
0,032
|
0,136
|
0,529
|
|
|
|
Чугун
|
|
0,072
|
0,142
|
0,490
|
|
|
|
Сталь
|
|
0,02
|
0,089
|
0,24
|
|
|
|
титановый сплав
|
|
0,041
|
0,104
|
0,882
|
|
|
|
Шпиндель
|
|
0,046
|
0,085
|
0,293
|
|
|
|
Шпонка
стальная
|
P(10
лет)=0,999
|
|
|
|
|
|
|
Клапаны обратные
Наименование
элементов и узлов арматуры
|
Вероятность безотказной работы
P(t*)
|
Данные эксплуатации
|
Данные испытаний ЦКБА
|
λoi·10-6 1/час
|
λoi·10-6 1/цикл
|
наименьшее
|
среднее
|
наибольшее
|
наименьшее
|
среднее
|
наибольшее
|
1
|
2
|
3
|
4
|
5
|
6
|
7
|
8
|
Винт
стопорный
|
P(10
лет)=0,999
|
|
|
|
|
|
|
Гайка
|
P(10
лет)=0,9995
|
|
|
|
|
|
|
Диск
(захлопка)
|
|
|
|
|
|
|
|
Стальной
|
|
0,004
|
0,13
|
0,83
|
|
|
|
Чугунный
|
|
0,011
|
0,29
|
0,65
|
|
|
|
Золотник
|
|
|
|
|
|
|
|
Стальной
|
|
0,08
|
0,27
|
0,78
|
|
|
|
Чугунный
|
|
0,17
|
0,32
|
0,62
|
|
|
|
из цветных сплавов
|
|
0,21
|
0,30
|
0,65
|
|
|
|
Корпус
|
|
|
|
|
|
|
|
Стальной
|
P(10
лет)=0,9995
|
|
|
|
|
|
|
Чугунный
|
P(10
лет)=0,999
|
|
|
|
|
|
|
из цветных сплавов
|
P(7
лет)=0,9995
|
|
|
|
|
|
|
Крышка
|
|
|
|
|
|
|
|
сталь
|
P(10
лет)=0,9995
|
|
|
|
|
|
|
Чугун
|
P(10
лет)=0,999
|
|
|
|
|
|
|
из цветных сплавов
|
P(7
лет)=0,9995
|
|
|
|
|
|
|
Муфта резьбовая
|
P(10
лет)=0,9995
|
|
|
|
|
|
|
Ось
|
P(10
лет)=0,9994
|
|
|
|
|
|
|
Прокладка
|
|
|
|
|
|
|
|
медь, сталь
|
|
0,009
|
0,11
|
0,24
|
|
|
|
фторопласт
|
|
0,12
|
0,22
|
0,34
|
|
|
|
паронит, резина
|
|
0,14
|
0,37
|
0,49
|
|
|
|
Пара трения
|
|
0,041
|
0,072
|
0,128
|
|
|
|
Пружина
|
|
0,051
|
0,076
|
0,114
|
|
|
|
Рычаг
|
|
0,009
|
0,052
|
0,123
|
|
|
|
Сильфон
|
P(t*) по ГОСТ 21744-83, ОСТ
26-07-2019-81
|
|
|
Серьга
|
|
0,006
|
0,0095
|
0,014
|
|
|
|
Соединение
|
|
|
|
|
|
|
|
Резьбовое
|
|
0,076
|
0,11
|
0,240
|
|
|
|
Сварное
|
|
0,021
|
0,056
|
0,101
|
|
|
|
Крепежное
|
|
0,009
|
0,017
|
0,023
|
|
|
|
Механическое
|
|
0,008
|
0,10
|
0,238
|
|
|
|
Сетка (фильтр)
|
|
0,041
|
0,072
|
0,128
|
|
|
|
Уплотнительные поверхности (кольца)
корпуса, золотника, диска
|
|
|
|
|
|
|
|
твердый сплав
|
|
0,02
|
0,17
|
0,43
|
|
|
|
Латунь
|
|
0,009
|
0,25
|
0,563
|
|
|
|
Фторопласт
|
|
0,093
|
0,37
|
0,624
|
|
|
|
резина
|
|
0,086
|
0,43
|
0,82
|
|
|
|
Фланец
|
P(10
лет)=0,999
|
|
|
|
|
|
|
Шпилька
|
P(10
лет)=0,999
|
|
|
|
|
|
|
Штифт
|
|
0,004
|
0,015
|
0,049
|
|
|
|
Шариковый
подшипник
|
|
0,11
|
0,27
|
0,53
|
13,0
|
15,0
|
17,0
|
Сальниковый
узел
|
|
0,010
|
0,014
|
0,024
|
|
|
|
Клапаны предохранительные
Наименование
элементов и узлов арматуры
|
Вероятность безотказной работы
P(t*)
|
Данные эксплуатации
|
Данные испытаний
|
λoi·10-6 1/час
|
λoi·10-6 1/цикл
|
наименьшее
|
среднее
|
наибольшее
|
наименьшее
|
среднее
|
наибольшее
|
1
|
2
|
3
|
4
|
5
|
6
|
7
|
8
|
Винт
регулировочный
|
|
0,11
|
0,25
|
0,98
|
|
|
|
Втулка
дискодержатель
|
|
0,11
|
0,24
|
0,45
|
|
|
|
Груз
|
|
0,003
|
0,008
|
0,021
|
|
|
|
Золотник
диск
|
|
0,42
|
0,79
|
0,98
|
|
|
|
Кольцо
регулировочное
|
P(10
лет)=0,9997
|
|
|
|
|
|
|
Корпус
|
|
|
|
|
|
|
|
стальной
|
P(10
лет)=0,9999
|
|
|
|
|
|
|
чугунный
|
P(10
лет)=0,9998
|
|
|
|
|
|
|
Крышка
|
|
|
|
|
|
|
|
стальная
|
P(10
лет)=0,9999
|
|
|
|
|
|
|
Чугунная
|
P(10
лет)=0,9998
|
|
|
|
|
|
|
Палец
|
|
0,062
|
0,084
|
0,101
|
|
|
|
Поверхность
трения
|
|
0,41
|
0,72
|
1,121
|
|
|
|
Прокладка
|
|
|
|
|
|
|
|
Фторопластовая
|
|
0,071
|
0,097
|
0,121
|
|
|
|
Резиновая
|
|
0,082
|
0,104
|
0,201
|
|
|
|
Паранитовая
|
|
0,060
|
0,109
|
0,297
|
|
|
|
Мембрана
|
P(10
лет)=0,9907
|
0,076
|
0,107
|
0,236
|
|
|
|
Пружина
|
P(10
лет)=0,9984
|
|
|
|
|
|
|
Рычаг
|
P(10
лет)=0,9996
|
|
|
|
|
|
|
Ручной дублер
|
P(10
лет)=0,9999
|
|
|
|
|
|
|
Сальник
|
|
0,012
|
0,052
|
0,158
|
|
|
|
Седло объемное
|
P(10
лет)=0,9995
|
0,004
|
0,017
|
0,16
|
|
|
|
Сильфон
|
P(t*)
по ГОСТ 21744-83 или ОСТ
26-07-2019-81
|
Соединение
|
|
|
|
|
|
|
|
Сварное
|
P(10
лет)=0,998
|
|
|
|
|
|
|
Резьбовое
|
P(10
лет)=0,9997
|
|
|
|
|
|
|
Механическое
|
P(10
лет)=0,9997
|
|
|
|
|
|
|
Крепежное
|
P(10
лет)=0,9997
|
|
|
|
|
|
|
Уплотнительные
кольца седла золотники
|
|
|
|
|
|
|
|
твердый сплав
|
|
0,42
|
0,63
|
0,98
|
|
|
|
Латуньt бронза
|
|
0,36
|
0,82
|
1,23
|
|
|
|
Фторопласт
|
|
0,51
|
0,84
|
1,04
|
|
|
|
Фильтр
|
P(10
лет)=0,994
|
|
|
|
|
|
|
Фланец
|
P(10
лет)=0,9995
|
|
|
|
|
|
|
Цилиндр
(стакан)
|
P(10
лет)=0,9968
|
|
|
|
|
|
|
Шток
|
P(10
лет)=0,9974
|
|
|
|
|
|
|
Шпилька
|
P(10
лет)=0,9994
|
|
|
|
|
|
|
Шарнирное соединение
|
P(10
лет)=0,9987
|
|
|
|
|
|
|
Клапаны регулирующие и
запорно-регулирующие
Наименование
элемента, узла, клапана
|
Вероятность безотказной работы
P(t*)
|
Данные эксплуатации
|
Данные испытаний
|
λoi·10-6 1/час
|
λoi·10-6 1/цикл
|
наименьшее
|
среднее
|
наибольшее
|
наименьшее
|
среднее
|
наибольшее
|
1
|
2
|
3
|
4
|
5
|
6
|
7
|
8
|
Болты
|
P(10
лет)=0,9987
|
|
|
|
|
|
|
Втулка
резьбовая
|
|
0,012
|
0,095
|
0,206
|
10,7
|
11,4
|
11,9
|
Гайка
накидная
|
|
0,036
|
0,082
|
0,132
|
10,2
|
10,5
|
12,3
|
Гайки
крепежные
|
P(10
лет)=0,999
|
|
|
|
|
|
|
Диафрагма
|
|
0,12
|
0,53
|
0,84
|
|
|
|
Диск
поворотный
|
|
0,52
|
0,97
|
3,04
|
|
|
|
Золотник
|
|
0,44
|
1,01
|
2,57
|
|
|
|
Корпус
|
|
|
|
|
|
|
|
стальной
|
P(10
лет)=0,999
|
|
|
|
|
|
|
Чугунный
|
P(10
лет)=0,9985
|
|
|
|
|
|
|
Цветные металлы
|
P(7
лет)=0,9978
|
|
|
|
|
|
|
Крепежные детали
|
P(10
лет)=0,9985
|
|
|
|
|
|
|
Крышка
|
|
|
|
|
|
|
|
Сталь
|
P(10
лет)=0,999
|
|
|
|
|
|
|
Бронза
|
P(7
лет)=0,9985
|
|
|
|
|
|
|
Мембрана.
|
|
0,08
|
0,93
|
3,45
|
|
|
|
Муфта
|
|
0,021
|
0,063
|
0,95
|
|
|
|
Направляющая
|
|
0,11
|
0,42
|
0,65
|
|
|
|
Плунжер
|
|
0,11
|
0,42
|
0,65
|
|
|
|
стержневой
|
|
0,09
|
0,51
|
1,32
|
13,6
|
15,8
|
16,4
|
Полый
|
|
0,11
|
0,72
|
2,65
|
15,8
|
20,1
|
24,2
|
Сегментный
|
|
0,14
|
0,45
|
0,98
|
9,62
|
12,2
|
20,1
|
Поршневой
|
|
0,22
|
0,64
|
1,32
|
12,1
|
17,3
|
23,4
|
Поверхность трения
|
|
0,027
|
0,52
|
1,48
|
11,6
|
4,79
|
3,41
|
Поршень
|
|
0,08
|
0,20
|
0,35
|
|
|
|
Прокладка
|
|
|
|
|
|
|
|
Фторопластовая
|
|
0,005
|
0,011
|
0,019
|
|
|
|
Резиновая
|
|
0,010
|
0,022
|
0,035
|
|
|
|
Паронитная
|
|
0,003
|
0,040
|
0,077
|
|
|
|
Пружина
|
P(10
лет)=0,999
|
0,012
|
0,024
|
0,065
|
|
|
|
Рычаг
|
P(10
лет)=0,998
|
0,009
|
0,021
|
0,058
|
|
|
|
Сальник
|
|
0,036
|
0,088
|
0,242
|
9,1
|
10,3
|
12,4
|
Седло
|
|
0,67
|
1,04
|
1,29
|
|
|
|
Соединение
|
|
|
|
|
|
|
|
Сварное
|
P(10
лет)=0,997
|
|
0,025
|
|
|
|
|
Резьбовое
|
P(10
лет)=0,998
|
|
0,021
|
|
|
|
|
Сильфон
|
P(t*)
по ГОСТ 21744-83 или ОСТ 26-07-2019-81
|
Уплотнение корпуса (уплотнительные кольца)
|
|
|
|
|
|
|
|
Стальное
|
P(10
лет)=0,9928
|
0,42
|
0,63
|
0,91
|
|
|
|
твердый сплав
|
P(10
лет)=0,9934
|
0,31
|
0,56
|
0,92
|
|
|
|
Уплотнение плунжера
|
|
|
|
|
|
|
|
Стальное
|
|
0,42
|
0,65
|
0,90
|
|
|
|
твердый сплав
|
|
0,39
|
0,48
|
0,86
|
|
|
|
Фторопластовое
|
|
0,21
|
0,37
|
0,96
|
|
|
|
Резиновое
|
|
0,71
|
0,84
|
0,98
|
|
|
|
Фланец
|
P(10
лет)=0,999
|
|
|
|
|
|
|
Шар
|
|
0,03
|
0,07
|
0,12
|
|
|
|
Шибер
|
|
0,61
|
0,82
|
0,96
|
|
|
|
Шланг
|
|
0,11
|
0,32
|
0,45
|
|
|
|
Шток
|
|
0,031
|
0,067
|
0,157
|
7,95
|
8,0
|
8,15
|
Шпиндель
|
|
0,035
|
0,085
|
0,162
|
9,5
|
10,0
|
10,6
|
Штуцер
|
P(10
лет)=0,999
|
|
|
|
|
|
|
Приводы (кроме электромагнитного)
Наименование
элемента привода
|
Вероятность безотказной работы
P(t*)
|
Данные эксплуатации
|
Данные испытаний
|
λoi·10-6 1/час
|
λoi·10-6 1/цикл
|
наименьшее
|
среднее
|
наибольшее
|
наименьшее
|
среднее
|
наибольшее
|
1
|
2
|
3
|
4
|
5
|
6
|
7
|
8
|
Гайка ходовая
|
|
0,072
|
0,095
|
0,13
|
|
|
|
Диафрагма
|
|
|
|
|
|
|
|
Зубчатая
передача
|
|
0,026
|
0,27
|
1,36
|
|
|
|
Клемма
|
|
0,003
|
0,005
|
0,009
|
|
|
|
Корпус
|
P(10
лет)=0,999
|
|
|
|
|
|
|
Кривошип
|
|
0,76
|
0,99
|
1,27
|
|
|
|
Крышка
|
P(10
лет)=0,999
|
|
|
|
|
|
|
Манжета
|
|
0,62
|
0,84
|
1,01
|
|
|
|
Мембрана
|
|
0,42
|
0,97
|
1,35
|
10,8
|
11,2
|
11,7
|
Муфта
|
|
0,21
|
0,40
|
0,65
|
|
|
|
Поршень
|
|
0,36
|
0,42
|
0,58
|
|
|
|
Пружина
|
|
0,031
|
0,076
|
0,125
|
|
|
|
Путевой выключатель (блок)
|
P(10
лет)=0,996
|
0,012
|
0,021
|
0,039
|
|
|
|
Редуктор
|
|
0,026
|
0,74
|
0,152
|
|
|
|
Соединение
|
|
|
|
|
|
|
|
Кулачковое
|
|
0,09
|
0,24
|
0,65
|
13,0
|
15,0
|
19,0
|
Шарнирное
|
|
0,80
|
2,4
|
4,0
|
|
|
|
Крепежное
|
|
0,008
|
0,017
|
0,025
|
|
|
|
Пневматическое
|
|
0,020
|
0,15
|
0,20
|
|
|
|
Контактное
|
|
0,002
|
0,01
|
0,02
|
|
|
|
Уплотнение ввода кабеля
|
P(10
лет)=0,998
|
|
|
|
|
|
|
Цилиндр
|
|
0,022
|
0,040
|
0,062
|
|
|
|
Шестерня
|
|
0,53
|
0,89
|
1,14
|
|
|
|
Шток
|
•
|
0,026
|
0,067
|
0,093
|
7,95
|
8,0
|
8,1
|
Электродвигатель
по соответствующим ТУ или другой
НТД.
|
Примечание. Показатели
надежности применять: для МИМ по ТУ 26-07-130-75, ТУ 26-07-1116-86, для ПОУ -
по ТУ 26-07-1096-79, электроприводы по соответствующим ТУ.
Приложение 3(Справочное). Значения
коэффициента а1
Наименование
элементов и узлов
|
а1
|
Резьбовое
соединение
Механическое
соединение
Поверхность
трения
Подшипник
Шпоночное
соединение
Пружина возвратная
Кулачковое
соединение
Зубчатая
передача
Магнит
и электромагнит
Катушка, клейма
Штифтовое
соединение
Прочие
элементы, работающие в наиболее тяжелом
режиме
|
5
|
Клапанно-запорное устройство
Сальниковая
набивка
Скользящее
уплотнение (фторопласт)
Мембрана
Прокладка
Крепежные
детали
|
2
|
Корпус
Маховик
и рукоятка
Узел
крепления маховика и рукоятки
Прочие
элементы, работающие в наиболее легком режиме
|
1
|
Приложение 4(Справочное). Поправочные
коэффициенты, учитывающие уменьшение интенсивности отказов элементов a2
Наименование элементов
|
a2·10-3
|
Штепсельный
разъем
|
1,00
|
Переключатель
|
1,00
|
Электродвигатель
|
0,28
|
Реле
|
1,00
|
Механический,
гидравлический и пневматический элемент
|
1,00
|
Показатели надежности отдельных
элементов и узлов изделия
Таблица 1
Наименование элементов и узлов
|
λоi·10-6
1/час
|
m
|
a1
|
λ'i=λoi·m·a1·10-6
1/час
|
t',
час
|
a2
|
λ''i=a2·λ'i·10-9
1/час
|
t'',
час
|
|
|
|
|
|
|
|
|
|
Показатели надежности узлов и элементов
Таблица 2
Обозначение по схеме
|
Наименование элементов и узлов
|
λоi·10-6
1/час
|
m
|
a1
|
λ'i=λoi·m·a1·10-6
1/час
|
t',
час
|
a2
|
λ''i=
λ'i ·a2· 10-9
1/час
|
t'',
час
|
P(t)
|
|
|
|
|
|
|
|
|
|
|
|
Таблица 1
Наименование
детали и напряжения
|
Материал изготовления детали
|
Расчётное напряжение кгс/см2
MSi
|
Допускаемое
напряжение кгс/см2
MRi
|
Коэффициент запаса

|
Коэффициент вариации прочности
kRi
|
Коэффициент
вариации нагрузки
kSi
|
Вероятность
безотказной работы детали при I-м напряжении

|
1
|
2
|
3
|
4
|
5
|
6
|
7
|
8
|
|
|
|
|
|
|
|
|
Таблица 2
Параметр функционирования.
|
Среднее значение параметра
yi
|
Ограничения параметра
[yВ,
yН]
|
Коэффициент вариации параметра
функционирования
kyi
|
Значения
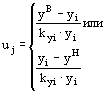
|
Вероятность безотказной работы
P2j=Ф(uj)
|
1
|
2
|
3
|
4
|
5
|
6
|
|
|
|
|
|
|
Приложение 7(Справочное) Классификатор отказов и предельных
состояний арматуры
КРАНЫ
Внешнее проявление отказа (критерии
отказа)
|
Отказавшие детали
|
Материал
|
Характер разрушения
|
1
|
2
|
3
|
4
|
Негерметичность затвора
|
Уплотнительные
кольца в корпусах шаровых кранов
|
Фторопласт 4
|
Износ, разрушение, трещины, отрыв
|
Резина
|
Износ, разрушение, разрыв, смятие, отрыв
|
Пробка, шар
|
Латунь, бронза, чугун, сталь, титановый сплав
|
Износ, задир, эррозия, коррозия, трещины, сколы, риски
|
Фаолит
|
Износ, разрушение, трещины, риски
|
Корпус
|
Латунь, чугун, сталь, титановый сплав
|
Износ, задир, эррозия, коррозия, трещины, сколы, риски
|
Негерметичность по отношению к
внешней среде
|
Корпус
|
Латунь, чугун, сталь, титановый сплав
|
Коррозия,
эррозия, трещины, разрыв, раковины, поры
|
Накидная
гайка
|
Латунь
|
Трещины, разрыв
резьбы, износ
|
Сальниковая набивка
|
Асбест, ХБС, ХБП
|
Разрушение, расслоение
|
Маслобензостойкая
резина
|
Износ, разрушение, смятие, разрыв
|
Прокладка
|
Паронит, картон
|
Износ, разрушение, расслоение, смятие
|
Фторопласт 4
|
Износ, разрушение, трещины
|
Резина
|
Износ, разрушение, разрыв
|
Манжета гидропневмопривода
|
Маслостойкая
резина, вакуумная
резина
|
Износ, разрушение, разрыв, смятие
|
Отсутствие рабочих перемещений
|
Пробка, шар
|
Латунь, бронза,
чугун, сталь, титановый сплав
|
Коррозия, задир, разрушение
|
Шпонка
|
Сталь
|
Излом, срез
|
Зубчатые колеса, редуктора
|
Сталь
|
разрушение, излом, скол, износ зубьев
|
Шпиндель
|
Сталь
|
Разрушение,
излом, коррозия
|
Поршень пневмопривода
|
Сталь
|
Задир, обрыв(излом), коррозия,
разрушение
|
Шток пневмопривода
|
Сталь
|
Изгиб (деформация), коррозия,
разрушение
|
Цилиндр пневмопривода
|
Чугун
|
Задир, коррозия, разрушение
|
КЛАПАНЫ ОБРАТНЫЕ
(Подъемные,
поворотные, приемные, невозвратно-запорные)
Внешнее проявление
отказа (критерии отказа)
|
Отказавшие детали
|
Материалы
|
Характер разрушения
|
1
|
2
|
3
|
4
|
Негерметичность затвора
|
Уплотнительная поверхность (кольцо)
захлопки, золотника
|
Твердый сплав, латунь, сталь
|
Износ, коррозия, эрозия, трещины,
скол, отрыв
|
Уплотнительная поверхность корпуса
|
-"-
|
-"-
|
Фторопласт 4
|
Износ, трещины, смятие, разрушение
|
Резана
|
Износ, разрушение, разрыв
|
Пружина
|
Сталь
|
Износ (деформация)
|
Негерметичность по отношению к внешней среде
|
Корпус
|
Сталь, бронза, латунь, чугун,
титановый сплав
|
Коррозия, эрозия, разрыв, трещины,
раковины, поры
|
Крышка
|
Сталь, латунь, чугун, титановый сплав
|
Трещины, поры, раковины разрыв
|
Прокладка
|
Медь, сталь
|
Коррозия, разрушение
|
Паронит, картон
|
Разрушение, расслоение, смятие
|
Резина
|
Износ, разрыв, смятие,
разрушение
|
Фторопласт 4
|
Износ, трещины, разрушение
|
Сильфон
|
Сталь
|
Разрыв, трещины
|
Отсутствие рабочих перемещений
|
Захлопка
|
Сталь, чугун
|
Разрушение, коррозия, отрыв
|
Золотник
|
Сталь, бронза, латунь, чугун,
титановый сплав
|
Разрушение, коррозия, отрыв от штока
|
Фторопласт 4
|
Износ, разрушение, трещины, отрыв
|
Пружины
|
Сталь
|
Износ, (деформация), излом, коррозия
|
Ось, штифт
|
Сталь
|
Излом, срез, коррозия
|
Рычаг, серьга
|
Сталь
|
Коррозия, излом деформация, отрыв
|
Диск
|
Сталь, чугун
|
Разрушение, излом, коррозия
|
Резина
|
Износ, деформация, разрушение, разрыв
|
ЗАДВИЖКИ
Внешнее проявление
отказа (критерии отказа)
|
Отказавшие детали
|
Материалы
|
Характер разрушения
|
1
|
2
|
3
|
4
|
Негерметичность затвора
|
Уплотнительные кольца корпуса, клина,
дисков, шибера
|
Твердый сплав, латунь, сталь, бронза
|
Износ, задиры, трещины, скол,
коррозия, эрозия, риски, отрыв
|
Негерметичность по отношению к
внешней среде
|
Сальниковая набивка
|
Асбест, пенька, ФУМ-В
|
Разрушение, расслоение, разрыв
|
Фторопласт 4
|
Износ, разрушение, трещины
|
Корпус
|
Сталь, бронза, чугун
|
Коррозия, эрозия, трещины, поры,
раковины, разрыв
|
Крышка
|
Сталь, бронза, чугун
|
Разрыв, трещины, поры, раковины
|
Болты, гайки, шпильки
|
Сталь
|
Износ, срыв резьбы
|
Прокладка
|
Паронит, картон
|
Разрушение, расслоение, смятие,
разрыв
|
Асбестометаллическая, фторопласт 4,
алюминий
|
Износ, разрушение, трещины, смятие
|
Манжета пневмогидропривода
|
Резина
|
Износ, разрушение, разрыв, смятие
|
Отсутствие рабочих перемещений
|
Резьбовая втулка, резьбовая часть шпинделя
|
Бронза, сталь, латунь
|
Износ, срыв резьбы, коррозия
|
Клин, диски, шибер
|
Бронза, чугун, сталь, латунь
|
Разрушение,
излом, отрыв
|
Ось, грибок
|
Сталь
|
Разрушение,
излом, срез
|
Шпиндель
|
Сталь, латунь
|
Разрушение, излом, изгиб(деформация),
отрыв
|
Направляющая клина
|
Сталь, чугун
|
Износ, задир, трещины
|
Шпонка, стопорный винт
|
Сталь
|
Излом, срез,
срыв резьбы(винт)
|
Зубчатые колеса редуктора
|
Сталь, бронза
|
Разрушение, излом, скол, износ зубьев
|
Поршень пневмо-, гидропривода
|
Чугун
|
Износ, задир, отрыв, разрушение, коррозия
|
Шток пневмо-, гидропривода
|
Сталь
|
Износ, изгиб, коррозия, разрушение
|
Цилиндр пневмо-, гидропривода
|
Чугун, сталь
|
Износ, задир, коррозия
|
КЛАПАНЫ ПРЕДОХРАНИТЕЛЬНЫЕ (ГРУЗОВЫЕ,
РЫЧАЖНЫЕ)
Внешнее проявление
отказа (критериев отказа)
|
Отказавшие детали
|
Материалы
|
Характер разрушения
|
1
|
2
|
3
|
4
|
Негерметичность затвора
|
Уплотнительное кольцо корпуса
|
Твердый сплав, латунь, бронза
|
Износ, коррозия, эрозия, трещины,
скол, отрыв от кольца
|
Уплотнительное кольцо золотника
|
-"-
|
-"-
|
Фторопласт 4
|
Износ, трещины, разрушение, отрыв
|
Резина
|
Износ, разрушение, разрыв, отрыв
|
Пружина
|
Сталь
|
Износ, деформация, излом
|
Негерметичность по отношению к
внешней среде
|
Корпус
|
Сталь, латунь, чугун
|
Коррозия, эрозия, трещины, разрыв,
раковины, поры
|
Крышка
|
Сталь, чугун
|
-"-
|
Сильфон
|
Сталь
|
Разрыв, трещины
|
Прокладка
|
Паронит
|
Разрушение, расслоение, смятие
|
Фторопласт 4
|
Износ, трещина, смятие
|
Разина
|
Разрушение, разрыв, смятие
|
Алюминий!
|
Деформация, разрушение
|
Мембрана
|
Резина
|
Разрушение, разрыв, деформация
|
Фторопласт 4
|
Износ, трещины, разрушение
|
Отсутствие рабочих перемещений
|
Направляющая втулка
|
Бронза
|
Задир, коррозия, трещина
|
Пружина
|
Сталь
|
Разрушение, излом, деформация (износ)
|
Шток
|
Сталь
|
Отрыв, излом, коррозия
|
Палец
|
Сталь
|
Срез, излом, коррозия
|
Рычаг
|
Сталь
|
Коррозия, отрыв, излом
|
КЛАПАНЫ (ВЕНТИЛИ) РЕГУЛИРУЮЩИЕ
Внешнее проявление
отказа (критерии отказа)
|
Отказавшие детали
|
Материалы
|
Характер разрушения
|
1
|
2
|
3
|
4
|
Негерметичность затвора
|
Уплотнительное
кольцо плунжера (золотника)
|
Сталь, твердый сплав
|
Износ, коррозия, эрозия, трещина,
скол, отрыв
|
Резина
|
Износ, разрушение, разрыв
|
Фторопласт 4
|
Износ, разрушение, трещина
|
Уплотнительное
кольцо корпуса
|
Сталь, твердый сплав
|
Износ, коррозия, эрозия, скол, отрыв,
трещина
|
Пружина
|
Сталь
|
Разрушение, износ, деформация
|
Мембрана
|
Резина, фторопласт 4
|
Разрыв, износ
|
Негерметичность по отношению к
внешней среде
|
Корпус
|
Сталь, латунь
|
Коррозия, эрозия, трещины, разрыв,
раковины, поры
|
Сальниковая набивка
|
Асбест, ФУМ-В
|
Износ, разрушение, расслоение
|
Фторопласт 4
|
Износ, разрушение, трещины
|
Прокладка
|
Паронит
|
Износ, разрушение, расслоение смятие
|
Фторопласт 4
|
Износ, разрушение, трещины, смятие
|
Прокладка
|
Резина
|
Износ, разрушение, разрыв, смятие
|
Крышка
|
Сталь, бронза
|
Разрыв, трещины, поры, раковины
|
Накидная гайка
|
Бронза
|
Поры, раковины, разрыв, срыв резьбы
|
Сильфон
|
Сталь
|
Разрыв, трещины
|
Болты (шпильки) гайки
|
Сталь
|
Износ резьбы, срыв
|
Отсутствие рабочих перемещений
|
Плунжер (золотник)
|
Сталь, бронза
|
Разрушение,
коррозия, отрыв от штока
|
Фторопласт 4
|
Износ, разрушение, трещины
|
Направляющая
|
Сталь
|
Износ, задиры, трещины
|
Шток
|
Сталь, бронза
|
Отрыв от золотника, излом, коррозия
|
Резьбовая часть шпинделя
|
Сталь
|
Износ, срыв резьбы, коррозия
|
Резьбовая втулка
|
Бронза
|
-"-
|
Мембрана
|
Резина
|
Износ, деформация, разрыв
|
Пружина
|
Сталь
|
Износ, деформация, излом
|
КЛАПАНЫ (ВЕНТИЛИ) ЗАПОРНЫЕ, ОТСЕЧНЫЕ
Внешнее проявление
отказа (критерии отказа)
|
Отказавшие детали
|
Материалы
|
Характер разрушения
|
1
|
2
|
3
|
4
|
Негерметичность затвора
|
Уплотнительное кольцо корпуса,
золотника
|
Твердый сплав, латунь, сталь
|
Износ, коррозия, эрозия, трещины,
скол, задир, риски, отрыв кольца
|
Фторопласт 4
|
Износ, риски, трещины, разрушение,
смятие, отрыв
|
Резина, кожа
|
Износ, разрушение, разрыв, смятие
|
Пружина
|
Сталь
|
Износ (деформация), излом
|
Негерметичность по отношению к
внешней среде
|
Корпус
|
Чугун, сталь, латунь, бронза,
аллюминиевый сплав, монель-металл, титановый сплав
|
Коррозия, эрозия, трещины, ; разрыв,
раковины, поры
|
Сальниковая набивка
|
Асбест, ФУМ-B
|
Износ, разрушение, расслоение
|
Резина
|
Износ, разрушение, разрыв
|
Прокладка
|
Фибра, паронит
|
Разрушение,
расслоение, смятие, разрыв
|
резина
|
Износ, разрушение, разрыв, смятие
|
Сильфон
|
Полутомпак, бронза, сталь
|
Разрыв, трещины
|
Крышка
|
Чугун, сталь, латунь, бронза
|
Разрыв, трещины, поры, раковины
|
Болты, гайки
|
Сталь
|
Износ, срыв резьбы, коррозия
|
Отсутствие
рабочих перемещений
|
Резьбовая втулка
|
Бронза, латунь
|
Износ резьбы, срыв
|
Резьбовая часть шпинделя
|
Латунь, сталь, титановый сплав, монель-металл
|
Износ резьбы, срыв
|
Подшипники
|
Сталь
|
Износ, коррозия, разрыв кольца, трещины
|
Шпиндель
|
Латунь, сталь, титановый сплав, монэль-мэталл
|
Разрушение, отрыв (излом)
|
Шток
|
Сталь
|
Отрыв
от шпинделя, золотника, излом,
коррозия
|
Золотник
|
Сталь, латунь, бронза, монель-металл, чугун
|
Разрушение,
коррозия, отрыв от штока
|
Золотник
|
Сталь, латунь,
бронза, монель-металл, чугун
|
Разрушение, коррозия, отрыв от штока
|
Шпонка, стопорный винт
|
Сталь
|
Излом, срез
|
Мембрана
|
Сталь
|
Износ, излом, коррозия
|
Резина
|
Разрушение, разрыв, износ
|
Поршень пневмопривода
|
Сталь
|
Износ, задир, отрыв от штока, разрушение, коррозия;
|
Шток пневмопривода
|
Сталь
|
Износ, изгиб, коррозия, разрушение
|
Цилиндр
пневмопривода
|
Сталь
|
Износ, задир, коррозия
|
Диафрагма
|
Резина
|
Разрушение, износ, разрыв
|
Фторопласт 4, полиэтилен
|
Износ, трещины, излом
|
Зубчатые колеса редуктора
|
Сталь
|
Разрушение, излом, износ, скол зубьев
|
Изменение сопротивления изоляции катушки
электромагнитного привода относительно корпуса
|
Катушка электромагнитного привода
|
Провод обмоточный электроизоляционные
материалы
|
Разрушение изоляции
|
Приложение 8(Справочное)
Наименование параметра
|
Коэффициент вариации kyi.
|
Миним.
|
Среднее
|
Максимал.
|
1.
|
Гидравлическое сопротивление
|
0,06
|
0,12
|
0,25
|
2.
|
Время срабатывания
|
0,1
|
0,23
|
0,35
|
3.
|
Протечка в затворе
|
0,08
|
0,27
|
0,39
|
4.
|
Минимальное напряжение срабатывания
|
0,1
|
0,2
|
0,3
|
5.
|
Ток (напряжение) отпускания
электромагнитного привода
|
0,02
|
0,04
|
0,07
|
6.
|
Минимальный ток (напряжение)
срабатывания электромагнитного привода
|
0,01
|
0,04
|
0,07
|
7.
|
Потребляемая мощность
электромагнитного привода
|
0,04
|
0,06
|
0,09
|
8.
|
Стабильность выходного давления
регулятора давления
|
0,01
|
0,025
|
0,04
|
9.
|
Давление начала открытия клапана
обратного
|
0,10
|
0,15
|
0,20
|
10.
|
Давление настройки предохранительного
клапана
|
0,02
|
0,04
|
0,08
|
11.
|
Давление полного открытия клапана
обратного, предохранительного
|
0,02
|
0,03
|
0,04
|
12.
|
Давление обратной посадки клапана
предохранительного
|
0,03
|
0,05
|
0,07
|
13.
|
Коэффициент пропускной способности
регулирующих клапанов
|
0,10
|
0,25
|
0,40
|
14.
|
Коэффициент расхода
|
0,08
|
0,18
|
0,32
|
15.
|
Усилие выпрессовки золотника
|
0,10
|
0,15
|
0,20
|
16.
|
Усилие состыковки разъемных элементов
|
0,02
|
0,03
|
0,04
|
17.
|
Продел прочности конструкционных материалов (для деталей, изготовленных
литьем):
|
|
|
|
Сталь
и титановые сплавы
|
0,06
|
0,12
|
0,18
|
Алюминиевые сплавы и
сплавы цветных металлов
|
0,042
|
0,12
|
0,21
|
Приложение
9(Справочное) функция нормального распределения Ф(x)
Таблица
X
|
,00
|
,01
|
,02
|
,03
|
,04
|
,05
|
,06
|
,07
|
,08
|
,09
|
0,0
|
0,50000
|
0,50399
|
0,50798
|
0,51197
|
0,51595
|
0,51994
|
0,52392
|
0,52790
|
0,53188
|
0,53536
|
0,1
|
0,53983
|
0,54380
|
0,54776
|
0,55172
|
0,55567
|
0,55962
|
0,56356
|
0,56749
|
0,57142
|
0,57535
|
0,2
|
0,57926
|
0,58317
|
0,58706
|
0,59095
|
0,59483
|
0,59871
|
0,60257
|
0,60642
|
0,61026
|
0,61409
|
0,3
|
0,61791
|
0,62172
|
0,62552
|
0,62930
|
0,63307
|
0,63683
|
0,64058
|
0,64431
|
0,64803
|
0,65173
|
0,4
|
0,65542
|
0,65910
|
0,66276
|
0,66640
|
0,67003
|
0,67364
|
0,67724
|
0,68082
|
0,68439
|
0,68793
|
|
|
|
|
|
|
|
|
|
|
|
0,5
|
0,69146
|
0,69497
|
0,69847
|
0,70194
|
0,70540
|
0,70884
|
0,71226
|
0,71556
|
0,71904
|
0,72240
|
0,6
|
0 ,72575
|
0,72907
|
0,73237
|
0,73565
|
0,73891
|
0,74215
|
0,74537
|
0,74857
|
0,75175
|
0,75490
|
0,7
|
0 ,75804
|
0,76115
|
0,76424
|
0,76730
|
0,77035
|
0,77337
|
0,77637
|
0,77935
|
0,78230
|
0,78524
|
0,8
|
0,78814
|
0,79103
|
0,79389
|
0,79673
|
0,79955
|
0,80234
|
0,80511
|
0,80785
|
0,81057
|
0,81327,
|
0,9
|
0,81594
|
0,81859
|
0,82121
|
0,82381
|
0,82639
|
0,82894
|
0,83147
|
0,83398
|
0,83646
|
0,83891
|
|
|
|
|
|
|
|
|
|
|
|
1,0
|
0,84134
|
0,84375
|
0,84614
|
0,84850
|
0,85083
|
0,85314
|
0,85543
|
0,85769
|
0,85993
|
0,86214
|
1,1
|
0,86433
|
0,86650
|
0,86864
|
0,87076
|
0,87286
|
0,87493
|
0,87698
|
0,87900
|
0,88100
|
0,88298
|
1,2
|
0,88493
|
0,88686
|
0,88877
|
0,89065
|
0,89251
|
0,89435
|
0,89617
|
0,89796
|
0,89973
|
0,90147
|
1,3
|
0,90320
|
0,90490
|
0,90658
|
0,90824
|
0,90988
|
0,91149
|
0,91309
|
0,91466
|
0,91621
|
0,91774
|
1,4
|
0,91924
|
0,92073
|
0,92220
|
0,92364
|
0,92507
|
0,92647
|
0,92786
|
0,92922
|
0,93056
|
0,93189
|
|
|
|
|
|
|
|
|
|
|
|
1,5
|
0,93319
|
0,93448
|
0,93574
|
0,93699
|
0,93822
|
0,93943
|
0,94062
|
0,94179
|
0,94295
|
0,94408
|
1,6
|
0,94520
|
0,94630
|
0,94738
|
0,94845
|
0,94950
|
0,95053
|
0,95154
|
0,95254
|
0,95352
|
0,95449
|
1,7
|
0,95543
|
0,95637
|
0,95728
|
0,95818
|
0,95907
|
0,95994
|
0,96080
|
0,96164
|
0,96246
|
0,96327
|
1,8
|
0,96407
|
0,96485
|
0,96562
|
0,96638
|
0,96712
|
0,96784
|
0,96857
|
0,96926
|
0,96995
|
0,97062
|
1,9
|
0,97128
|
0,97193
|
0,97257
|
0,97320
|
0,97381
|
0,97441
|
0,97500
|
0,97558
|
0,97615
|
0,97670
|
|
|
|
|
|
|
|
|
|
|
|
2,0
|
0,97725
|
0,97778
|
0,97831
|
0,97882
|
0,97932
|
0,97982
|
0,98030
|
0,98077
|
0,98124
|
0,98169
|
2,1
|
0,98214
|
0,98257
|
0,98300
|
0,98341
|
0,98382
|
0,98422
|
0,98461
|
0,98500
|
0,98537
|
0,98574
|
2,2
|
0,93610
|
0,98645
|
0,98679
|
0,98713
|
0,98745
|
0,98778
|
0,98809
|
0,98840
|
0,98870
|
0,98899
|
2,3
|
0,98928
|
0,98956
|
0,98983
|
0,920097
|
0,920358
|
0,920613
|
0,920863
|
0,921105
|
0,921344
|
0,921576
|
2,4
|
0,92I803
|
0,922024
|
0,922240
|
0,922451
|
0,922656
|
0,922857
|
0,923056
|
0,923244
|
0,923431
|
0,923613
|
|
|
|
|
|
|
|
|
|
|
|
2,5
|
0,923790
|
0,923963
|
0,924132
|
0,924297
|
0,924457
|
0,924614
|
0,924766
|
0,924915
|
0,925060
|
0,925201
|
2,6
|
0,925339
|
0,925473
|
0,925604
|
0,925731
|
0,925855
|
0,925975
|
0,926093
|
0,926207
|
0,926319
|
0,926427
|
2,7
|
0,926533
|
0,926636
|
0,926736
|
0,926833
|
0,926928
|
0,927020
|
0,927110
|
0,927197
|
0,927282
|
0,927365
|
2,8
|
0,927445
|
0,927523
|
0,927599
|
0,927673
|
0,927744
|
0,927814
|
0,927882
|
0,927948
|
0,928012
|
0,928074
|
2,9
|
0,928134
|
0,928193
|
0,928250
|
0,928305
|
0,928359
|
0,928411
|
0,928462
|
0,928511
|
0,928559
|
0,928605
|
|
|
|
|
|
|
|
|
|
|
|
3,0
|
0,928650
|
0,928694
|
0,928736
|
0,928777
|
0,928817
|
0,928856
|
0,928893
|
0,928930
|
0,928965
|
0,928999
|
3,1
|
0,930324
|
0,930646
|
0,930957
|
0,931260
|
0,931553
|
0,931836
|
0,932112
|
0,932378
|
0,932636
|
0,932886
|
3,2
|
0,933129
|
0,933363
|
0,933590
|
0,933810
|
0,934024
|
0,934230
|
0,934429
|
0,934623
|
0,934810
|
0,934991
|
3,3
|
0,935166
|
0,935335
|
0,935499
|
0,935658
|
0,935811
|
0,935959
|
0,936103
|
0,936242
|
0,936376
|
0,936505
|
3,4
|
0,936631
|
0,936752
|
0,936869
|
0,936982
|
0,937091
|
0,937197
|
0,937299
|
0,937398
|
0,937493
|
0,937585
|
|
|
|
|
|
|
|
|
|
|
|
3,5
|
0,937674
|
0,937759
|
0,937842
|
0,937922
|
0,937999
|
0,938074
|
0,938146
|
0,938215
|
0,938282
|
0,938347
|
3,6
|
0,938409
|
0,938469
|
0,938527
|
0,938583
|
0,938637
|
0,938689
|
0,938739
|
0,938787
|
0,938834
|
0,938879
|
3,7
|
0,938922
|
0,938964
|
0,940039
|
0,940426
|
0,940799
|
0,941158
|
0,941504
|
0,941838
|
0,942159
|
0,942468
|
3,8
|
0,942765
|
0,943052
|
0,943327
|
0,943593
|
0,943848
|
0,944094
|
0,944331
|
0,944558
|
0,944777
|
0,944978
|
3,9
|
0,945190
|
0,945385
|
0,945573
|
0,945753
|
0,945926
|
0,946092
|
0,946253
|
0,946406
|
0,946554
|
0,946696
|
|
|
|
|
|
|
|
|
|
|
|
4,0
|
0,946833
|
0,946964
|
0,947090
|
0,947211
|
0,947327
|
0,947439
|
0,947546
|
0,947949
|
0,947748
|
0,947843
|
4,1
|
0,947934
|
0,948022
|
0,948106
|
0,948186
|
0,948263
|
0,948338
|
0,948409
|
0,948477
|
0,948542
|
0,948605
|
4,2
|
0,948665
|
0,948723
|
0,948778
|
0,948832
|
0,948883
|
0,948931
|
0,948978
|
0,950226
|
0,950655
|
0,951066
|
4,3
|
0,951460
|
0,951837
|
0,952199
|
0,952545
|
0,952876
|
0,953193
|
0,953497
|
0,953788
|
0,954066
|
0,954332
|
4,4
|
0,954587
|
0,954831
|
0,955065
|
0,955288
|
0,955502
|
0,955706
|
0,955902
|
0,956089
|
0,956268
|
0,956439
|
|
|
|
|
|
|
|
|
|
|
|
4,5
|
0,956602
|
0,956759
|
0,956908
|
0,957051
|
0,957187
|
0,957318
|
0,957442
|
0,957561
|
0,957665
|
0,957784
|
4,6
|
0,957888
|
0,957937
|
0,958081
|
0,958172
|
0,958258
|
0,958340
|
0,958419
|
0,958494
|
0,958566
|
0,958634
|
4,7
|
0,958699
|
0,958761
|
0,958821
|
0,958877
|
0,958931
|
0,958983
|
0,960320
|
0,960789
|
0,961235
|
0,961661
|
4,8
|
0,962067
|
0,962453
|
0,962822
|
0,963173
|
0,963508
|
0,963827
|
0,964131
|
0,964420
|
0,964696
|
0,964958
|
4,9
|
0,965208
|
0,965446
|
0,965673
|
0,965889
|
0,966094
|
0,966289
|
0,966475
|
0,966652
|
0,966821
|
0,966981
|
|
|
|
|
|
|
|
|
|
|
|
5,0
|
0,967133
|
0,967288
|
0,967416
|
0,967548
|
0,967672
|
0,967791
|
0,967904
|
0,968011
|
0,968113
|
0,968210
|
5,1
|
0,968302
|
0,968389
|
0,968472
|
0,968551
|
0,968626
|
0,968698
|
0,968765
|
0,968830
|
0,968891
|
0,968949
|
5,2
|
0,970036
|
0,970558
|
0,971054
|
0,971524
|
0,971971
|
0,972395
|
0,972797
|
0,973179
|
0,973541
|
0,973884
|
5,3
|
0,974210
|
0,974519
|
0,974812
|
0,975089
|
0,975353
|
0,975602
|
0,975839
|
0,976063
|
0,976276
|
0,976477
|
5,4
|
0,976668
|
0,976849
|
0,977020
|
0,977182
|
0,977336
|
0,977482
|
0,977619
|
0,977750
|
0,977873
|
0,977990
|
|
|
|
|
|
|
|
|
|
|
|
5,5
|
0,978101
|
0,978206
|
0,978305
|
0,978399
|
0,978488
|
0,978572
|
0,978651
|
0,978726
|
0,978797
|
0,978865
|
5,6
|
0,978928
|
0,978988
|
0,979045
|
0,979099
|
0,979150
|
0,979198
|
0,979243
|
0,979286
|
0,979327
|
0,979365
|
5,7
|
0,979401
|
0,979435
|
0,979467
|
0,979498
|
0,979527
|
0,979554
|
0,979579
|
0,979604
|
0,979626
|
0,979648
|
5,8
|
0,979668
|
0,979688
|
0,979706
|
0,979723
|
0,979739
|
0,979754
|
0,979769
|
0,979782
|
0,979795
|
0,979807
|
5,9
|
0,979818
|
0,979829
|
0,979839
|
0,979849
|
0,979857
|
0,979866
|
0,979878
|
0,979881
|
0,979888
|
0,979896
|
|
|
|
|
|
|
|
|
|
|
|
6,0
|
0,979901
|
-
|
-
|
-
|
-
|
-
|
-
|
-
|
-
|
-
|
Приложение 10(Справочное) Коэффициенты
износостойкости материалов
Коэффициенты гидроабразивной износостойкости материалов
Сталь
|
Kи
|
Чугун и другие материалы
|
Kи
|
XI2
|
8,74
|
Ковкий
чугун
|
7,68
|
9X18
|
6,92
|
Высокопрочный
чугун
|
6,30
|
12XH3A
|
5,82
|
Серый
чугун
|
3,62
|
4X13
|
4,07
|
AМ48Ц
|
4,85
|
1X18H9T
|
3,97
|
И4Х12М
|
5,3
|
1X13
|
3,57
|
Резина
|
4,47
|
СтЗ
|
3,25
|
Фторопласт
|
1,15
|
Ст45
|
0,94
|
|
|
Коэффициенты газоабразивной
износостойкости материалов
Материал
|
Kи
|
Материал
|
Kи
|
Сталь
углеродистая
|
1,1
|
Чугун
легированный
|
1,24
|
Фторопласт
4
|
0,08
|
Сталь
Ст45
|
1,1
|
Полистирол
|
0,05
|
|
|
Твердые
сплавы
|
1,03
|
|
|
Коэффициенты относительной
износостойкости материалов
Материал (марка стали или сплава)
|
Kи
|
Материал
|
Kи
|
СтЗ
|
1.0
|
10Х14АГ15
|
5,30
|
10XCHД
|
1,35
|
10Х14Г14Н4Т
|
5,38
|
30ХГСА
|
1,02
|
07Х13АГ20
|
5,54
|
08X13
|
2,93
|
12X18H10T
|
6,0
|
20X13
|
5,27
|
Х19ГД
|
7,62
|
Скорость
коррозии материалов определяется по РТМ 26-07-225-79.
Пример 1. Расчет показателей
безотказности 1 методом
Настоящий
расчет распространяется на мембранный клапан с электромагнитным приводом
Т26000-050.
1. ЗАДАЧА РАСЧЕТА
Определить
вероятность безотказной работы клапана-с электромагнитным приводом Т26000-050 в
течение гарантийного срока 5 лет
2. ИСХОДНЫЕ ДАННЫЕ
Сборочный
чертеж изделия.
Гарантийная
наработка 100000 циклов при гарантийном сроке 5 лет.
Время
совершения одного цикла tц
= 10 сек.
3. ОСНОВНЫЕ ДОПУЩЕНИЯ, ПРИНЯТИЕ ПРИ
РАСЧЕТЕ
3.1.
Отказы элементов являются событиями случайными и независимыми.
3.2.
Вероятность безотказной работы элементов определяется экспоненциальным законом.
3.3.
Все элементы одного и того же типа равнонадежны, то есть интенсивность отказов
однотипных элементов одинакова.
3.4. Из
рассмотрения исключаются периоды приработки и износа, то есть интенсивность
отказов принимается постоянной.
3.5.
При расчете учитываются только те элементы, выход из строя которых приводит к
отказу всего изделия.
4. РАСЧЕТ ПОКАЗАТЕЛЕЙ БЕЗОТКАЗНОСТИ
4.1.
Надежность элементов, находящихся непрерывно
под нагрузкой, независимо от того, совершается рабочий цикл или нет, рассчитывается на гарантийный срок, указанный в
задании, то есть на время
t = 5 лет ≈ 43800 час
4.2.
Надежность элементов, находящихся под нагрузкой только в течение рабочего цикла, рассчитывается на полное время совершения общего числа циклов,
указанных в задании (гарантийная наработка), определяемое по формуле:

где T-
|
гарантийная наработка;
|
tц-
|
время совершения одного цикла (tц = 10 сек по данным
конструкторских отделов).
|
4.3.
Надежность элементов, находящихся под нагрузкой в тот момент, когда запорное
устройство открыто, рассчитывается на время, определяемое по формуле:

где to-
|
время, в течение которого запорное устройство открыто (to
= 200 сек по данным конструкторских отделов)
|
4.4.
Надежность элементов, находящихся под нагрузкой в тот момент, когда запорное устройство
закрыто, рассчитывается на время t'3, определяемое по формуле:

4.5.
Время работы ручного дублера tд= 420 час (по данным
конструкторских отделов).
4.6.
При расчете учитываются только те элементы, выход из строя которых приводит к
отказу всего изделия,
4.7.
Расчет проектной вероятности безотказной работы клапана производится исходя из
основной количественной характеристики надежности - интенсивности отказов.
4.8.
Интенсивность отказов работающего элемента определяется по формуле:

где λo-
|
номинальная интенсивность отказов работающего под
нагрузкой элемента;
|
а1-
|
коэффициент, учитывающий условия эксплуатации.
|
4.9.
Интенсивность отказов ненагруженного элемента определяется по формуле:

где а2-
|
поправочный коэффициент, учитывающий уменьшение
интенсивности отказов ненагруженного элемента а2 = 1·10-3
|
4.10.
Вероятность безотказной работы элемента определяется по формуле:
а) для
элементов, находящихся под нагрузкой в течение всего времени t
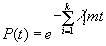
где m-
|
число элементов i-го типа;
|
б) для
элементов, находящихся под нагрузкой в течении времени t' и не находящихся под нагрузкой
в течении t"
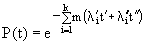
где t = t'+t"
4.11.
Общая логическая схема соединения узлов:

А -
узел клапана;
Б -
узел ручного дублера;
В -
узел электромагнитного привода.
4.12.
Вероятность безотказной работы изделия определяется по формуле:

где PА, PБ, PВ-
|
вероятность безотказной работы
узлов А, Б, В соответственно.
|
4.13.
Для расчета вероятности безотказной работы
заполняется таблица.
4.14.
Вероятность безотказной работы элементов,
работающих в течение времени t = 43800 час, определяется по формулам:
а) для
узла А

б) для
узла Б

в) для
узла В

Наименование элементов и узлов
|
,
час-1
|
m
|
а1
|
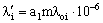
1/час
|
t',
час
|
a2
|

1/час
|
t",
час
|
А.
Узел клапана
|
1.
|
Корпус стальной
|
0,9995
(10 лет)
|
P(5
лет) = 0,99974
|
2.
|
Резьбовое соединение гайка-золотник
|
0,090
|
1
|
5
|
0,45
|
43800
|
1·10-3
|
0,45
|
-
|
3.
|
Прокладка
|
0,0096
|
2
|
1
|
0,0192
|
43800
|
0,0192
|
-
|
4.
|
Клапанно-запорное устройство
|
0,13
|
1
|
2
|
0,26
|
5560
|
0,26
|
38240
|
5.
|
Поверхность трения
корпус-направляющая
|
0,072
|
1
|
5
|
0,360
|
280
|
0,360
|
43520
|
Наименование элементов и узлов
|
,
час-1
|
m
|
а1
|

1/час
|
t',
час
|
a2
|
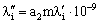
1/час
|
t",
час
|
Б.
Узел ручного дублера
|
1.
|
Резьбовое соединение корпус-винт
аварийный
|
0,09
|
1
|
5
|
0,45
|
420
|
1·10-3
|
0,45
|
43380
|
2.
|
Поверхность
трения корпус-кольцо
|
0,042
|
1
|
5
|
0,36
|
420
|
0,36
|
43380
|
3.
|
Механическое
соединение винт-корпус
|
0,086
|
1
|
5
|
0,43
|
420
|
0,43
|
43380
|
4.
|
Кольцо (уплотнение скользящее)
|
0,22
|
1
|
1
|
0,22
|
43800
|
0,22
|
-
|
5.
|
Прокладка
|
0,0056
|
1
|
1
|
0,0056
|
43800
|
0,0056
|
-
|
Наименование элементов и узлов
|
,
час-1
|
m
|
а1
|
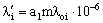
1/час
|
t',
час
|
a2
|

1/час
|
t",
час
|
В.
Узел электромагнитного привода
|
1.
|
Уплотнение ввода
|
P(10
лет) = 0,999
|
P(5
лет) = 0,9995
|
2.
|
Уплотнительное
|
0,0056
|
3
|
2
|
0,0336
|
43800
|
|
0,0336
|
-
|
3.
|
Катушка
|
0,014
|
1
|
5
|
0,070
|
5560
|
0,070
|
38240
|
4.
|
Клеммы
|
0,004
|
2
|
5
|
0,040
|
5560
|
0,040
|
38240
|
5.
|
Пружина
|
P(10
лет) = 0,9998
|
P(5
лет) = 0,9999
|
6.
|
Уплотнение скользящее
|
0,27
|
1
|
1
|
0,27
|
38240
|
0,1·10-3
|
0,27
|
5560
|
7.
|
Поверхность трения сердечник-трубка в
сборе
|
0,072
|
1
|
5
|
0,360
|
280
|
0,360
|
43520
|
4.15.
Вероятность безотказной работы элементов, работающих в точение времени t'1=280
час определяется по формулам:
а) для
узла А

б) для
узла В

4.16.
Вероятность безотказной работы элементов, нагруженных в течение времени t'2
= 5560 час определяется по формулам:
а) для
узла А

б) для
узла В

4.17.
Вероятность безопасной работы элементов, нагруженных в течение времени t'3
= 38240 час определяется по формуле для узла В:

4.18.
Вероятность безотказной работы элементов, работающих в течение времениt t4=tд=420 час, определяется по формуле для узла Б:

4.19. Вероятность
безотказной работы элементов,
ненагруженных в течение времени
t"1=43800-280=43520
час определяется по формуле:
а) для
узла А

б) для
узла В

4.20.
Вероятность безотказной работы элементов, ненагруженных в течение времени
t"2=43800-5560=38240
час., определяется по формулам:
а) для
узла А

б) для
узла В

4.21.
Вероятность безотказной работы элементов, ненагруженных в течение времени
t"3=43800-38240=5560 час, определяется по
формуле:

4.22.
Вероятность безотказной работы элементов, не работающих в течение времени
t"4=43800-420=43380 час, определяются по
формуле

4.23.
Вероятность безотказной работы корпуса Рк, уплотнения ввода Рув и пружкны
Рп определяются по формуле




4.24.
Вероятность безотказной работы узла А
определяется по формуле:

4.25.
Вероятность безотказной работы узла Б определяется по формуле:

4.26.
Вероятность безотказной работы узла В определяется по формуле:

4.27.
Вероятность безотказной работы, изделия в целом определяется по формуле:

5. ЗАКЛЮЧЕНИЕ
Предполагаемая вероятность безотказной работы мембранного клапана с электромагнитным приводом в течение
гарантийной наработки 100000 циклов при гарантийном сроке 5 лот
составляет 0,9777
Расчет является ориентировочным и должен быть
уточнен последующими испытаниями на
надежность или сбором статистических данных
о надежности изделия в процессе эксплуатации.
Пример 2 расчет показателей
безотказности 2 методом
Настоящий
расчет распространяется на
клапан отсечной угловой "НЗ" с электроприводом.
1. ЗАДАЧА РАСЧЕТА
Определить
вероятность безотказной работы клапана в течение назначенного ресурса за 30000
час - 500 циклов.
2. ИСХОДНЫЕ ДАННЫЕ
2.1.
Критерии отказов клапана:
- негерметичность относительно внешней
среды;
- негерметичность в затворе;
-
самопроизвольное закрытие;
-
самопроизвольное открытие;
-
отсутствие рабочих перемещений.
2.2.
Назначенный ресурс за период 4 года (30000 часов) - T = 500 циклов.
2.3. Клапан открыт ~ 50% to ≈
15.000 час.
2.4. Время совершения цикла 0,5 сек.
3. ОСНОВНЫЕ ДОПУЩЕНИЯ, ПРИНЯТЫЕ ПРИ
РАСЧЕТЕ
3.1.
Отказы элементов являются событиями случайными и независимыми.
3.2.
Вероятность безотказной работы элементов изделия определяется экспоненциальным
законом распределения.
3.3.
Все элементы одного и того же типа имеют
равную интенсивность отказов.
3.4. Из
рассмотрения исключаются периоды приработки и износа, т.е. интенсивность
отказов принимается постоянной.
3.5.
При расчете учитываются только те элементы, выход из строя которых приводит к отказу клапана.
4. РАСЧЕТ ПОКАЗАТЕЛЕЙ НАДЕЖНОСТИ
4.1.
Вероятность безотказной работы элементов, находящихся непрерывно под нагрузкой, рассчитывается на время
t
= 30000 час (500 циклов)
4.2.
Вероятность безотказной работы элементов, находящихся под нагрузкой в течение
времени совершения циклов,
определяется на время

4.3.
Вероятность безотказной работы
элементов, находящихся под нагрузкой, когда клапан открыт,
рассчитывается на время

4.4.
Вероятность безотказной работы элементов, находящихся под нагрузкой, когда
клапан закрыт, рассчитывается на время:

4.5.
Вероятность безотказной работы ненагруженных элементов рассчитывается на время



4.6.
Интенсивность отказов нагруженного элемента определяется по формуле:

где λo-
|
интенсивность отказов нагруженного элемента;
|
а1-
|
коэффициент, учитывающий
условия эксплуатации.
|
4.7.
Интенсивность отказов ненагруженного элемента
определяется по формуле:

где а2-
|
поправочный коэффициент, учитывающий уменьшение интенсивности отказов ненагруженного элемента.
|
4.8.
Вероятность безотказной работы (i j ) элемента определяется но
формуле
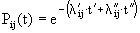
или по
формуле

если
исходной информацией о надежности элемента является вероятность безотказной работы элемента в течение периода t*
4.9.
Строим схему отказов клапана
отсечного (схема 1) и заполняем таблицу.
Схема 1
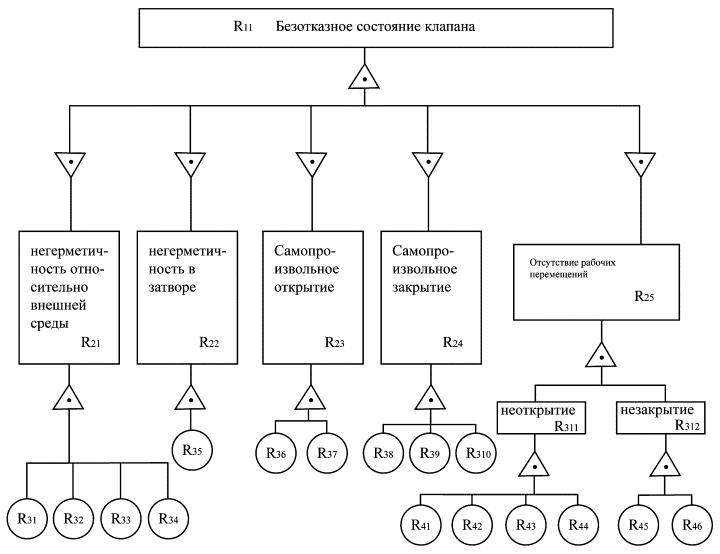
Таблица
Обозначение на схеме
|
Наименование
элемента, узла арматуры
|
,
1/час
|
m
|
а1
|
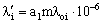
1/час
|
t',
час
|
a2
|

1/час
|
t",
час
|
P(t)
|
1
|
2
|
3
|
4
|
5
|
6
|
7
|
8
|
9
|
10
|
11
|
R41
|
Сильфон
125-8-0,3×6
38-12-0,2×4
|
P1(1500ц)=0,98
Р2(1500ц)=0,98
|
(по ГОСТ ВД 21744-83)
|
|
|

P2(500)=0,99328
P41=0,9866
|
R42
|
Сварное соединение
|
0,025
|
2
|
5
|
0,125
|
0,07
|
1·10-3
|
0,125
|
29999,93
|
P42
= exp[-2(0,125·10-6·0,07
+ 0,125·10-9·29999,93)] = 0,9999
|
R43
|
Резьбовое соединение
|
0,02
|
1
|
5
|
0,100
|
0,07
|
1·10-3
|
0,1
|
29999,93
|
P43
= exp[-(0,1·10-6·0,07 + 0,1·10-9·29999,93)] = 0,9999
|
R44
|
Пара трения:
шток-втулка,
втулка-стойка, корпус-золотник
|
0,52
|
3
|
5
|
2,6
|
0,07
|
1·10-3
|
2,6
|
29999,93
|
Р44
= eхр[-3(2,6·10-6·0,07
+ 2,6·10-9·29999,93)] = 0,9999
|
R45
|
Электропривод
|
0,97
|
(30000) час
|
(по 0ТТ-87)
|
|
|
P45
= 0,97
|
R46
|
Пара трения:
шток-втулка втулка-стойка корпус-золотник
|
0,52
|
3
|
5
|
2,6
|
0,07
|
0,1·10-3
|
2,6
|
29993,93
|
P46
= exp[-3(2,6·10-6·0,07 + 2,6·10-9·29999,93)] = 0,9999
|
R31
|
Сварное соединение:
втулка-корпус; сильфон-кольцо-втулка; золотник-сильфон
|
0,025
|
3
|
5
|
0,125
|
30000
|
|
|
-
|
P31(30000ч)
= ехр[-3 (0,125·10-6·30000)] = 0,9888
|
R32
|
Сильфон
|
P(1500ц)
= 0,98
|
(ГОСТ ВД 21744-83)
|
|
|

|
R33
|
Корпус
|
P(10
лет) =
|
0,9995
|
|
|
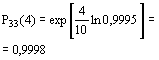
|
R34
|
Резьбовые соединения:
шпилька-гайка; шпилька-цилиндр
|
0,02
|
2
|
5
|
0,1
|
30000
|
|
|
|
P34(30000)=exp[-2·0,1·10-6-·30000] =0,9940
|
R35
|
Узел затвора
|
P(3000)
= 0,999
|
(ОСТ
26-07-1375-82)
|
|
|
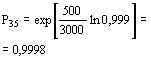
|
R36
|
Сильфон
|
P(1500ц) = 0,98
|
(ГОСТ
ВД 21744-83)
|
|
|

|
R37
|
Сварное
соединение:
сильфон-кольцо-втулка;
цилиндр-втулка
|
0,025
|
2
|
5
|
0,125
|
15000
|
0,1·10-3
|
0,125
|
15000
|
P37 =
exp[-2(0,125·10-6·15000
+ 0,125·10-9·15000)] = 0,9962
|
R38
|
Сильфон
125-8-0,3×6
38-12-0,2×4
|
P1(1500ц) = 0,98
Р2(1500ц)
= 0,98
|
(ГОСТ
ВД 21744-83)
|
|
|
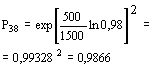
|
R39
|
Сварное
соединение:
сильфон-кольца-втулка;
сильфон-шток
сильфон-кольцо-цилиндр;
цилиндр-втулка
|
|
|
|
|
|
|
|
|
P39 =
exp[-4(0,125·10-6·15000
+ 0,125·10-9·15000)] = 0,9925
|
R310
|
Резьбовое
соединение:
Шток-втулка
|
0,02
|
1
|
5
|
0,1
|
15000
|
0,1·10-3
|
0,1
|
15000
|
P310 =
exp[-(0,125·10-6·15000
+ 0,125·10-9·15000)] = 0,9981
|
Определение
вероятности безотказной работы по видом отказа:
-
"неоткрытие"

-
"незакрытие"
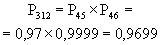
- Негерметичность относительно внешней
среды

- Негерметичность в затворе
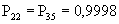
-
Самопроизвольное открытие

-
Самопроизвольное закрытие

-
Отсутствие рабочих перемещений

Вероятность
безотказной работы клапана отсечного углового "НЗ" * с
электроприводом в течение назначенного ресурса за 4 года (30000 часов) 500
циклов определим по формуле:

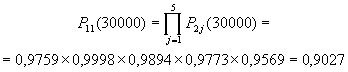
5. ЗАКЛЮЧЕНИЕ
Вероятность
безотказной работы клапана отсечного углового "НЗ" с электроприводом
в течение назначенного ресурса за 4 года (30000 час) 500 циклов составляет
0,9027
Расчет
является ориентировочным и должен быть уточнен последующими испытаниями на
надежность или сбором
статистических данных о надежности клапана в процессе эксплуатации.
Пример 3. Определение вероятности безотказной работы
3 методом
Настоящий
расчет выполнен душ клапана (затвора) обратного черт. K44136.100
1. ЗАДАЧА РАСЧЕТА
Определить
вероятность безотказной работы клапана в течение гарантийного срока 8000 час
(250 циклов).
2. ИСХОДНЫЕ ДАННЫЕ
1)
Сборочный чертеж изделия.
2)
Результаты силового и прочностного
расчета клапана.
3)
Коэффициенты вариации параметров работоспособности и механических свойств материалов,
применяемых в конструкции клапана.
3. ОСНОВНЫЕ ДОПУЩЕНИЯ, ПРИНЯТЫЕ ПРИ
РАСЧЕТЕ
1)
Прочность и нагрузка
распределены по нормальному закону
распределения.
4. РАСЧЕТ ПОКАЗАТЕЛЕЙ БЕЗОТКАЗНОСТИ
4.1.
Вероятность безотказной работы клапана обратного определим по формуле

где P1-
|
вероятность неразрушения клапана;
|
P2-
|
Вероятность невыхода значений параметров работоспособности
клапана за допустимые границы.
|
4.2.
Вероятность неразрушения клапана P1 определим как
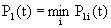
где P1i-
|
вероятность неразрушения
детали при действии i-й нагрузки»
|
4.3.
Вероятность P1i
рассчитываем
с помощью модели непревышения
типа "нагрузка-прочность" по формуле
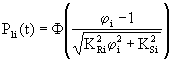
где Ф(…)-
|
функция нормального закона распределения ;
|
-
|
коэффициент запаса прочности;
|
KRi-
|
коэффициент вариации величины MRi;
|
KSi-
|
коэффициент вариации величины MSi;
|
Результаты
силового и прочностного расчета
клапана обратного и расчетные величины P1i сведены в таблицу 1.

4.4. Вероятность P2 рассчитывается с помощью модели
"непревышения" типа "параметр-поле допуска" по формула

где P2j-
|
вероятность невыхода i -го параметра
функционирования за допустимые пределы.
|
Параметрами
функционирования клапана
обратного являются:
- герметичность в затворе;
- давление открытия клапана;
- коэффициент гидравлического сопротивления.
Таблица 1
Наименование
детали и напряжения
|
Материал
|
Расчетное напряжение
кгc/cм2(MSi)
|
Допускаемое напряжение
кгс/см2(МRi)
|
Коэффициент
запаса

|
Коэффициент вариации прочности

|
Вероятность безотказной работы

|
ФЛАНЕЦ
|
Сталь 12X18H9T
|
|
|
|
|
|
Осевые напряжения
|
|
153
|
332
|
2,17
|

|
Ф(3,56)=0,9998
|
Радиальные напряжения
|
|
111
|
173
|
1,56
|
|
Ф(2,04)=0,9847
|
Кольцевые напряжения
|
|
89
|
173
|
1,94
|
|
Ф(3,06)=0,9988
|
КОРПУС
|
Сталь 12X18H9T
|
|
|
|
|
|
Приведенное напряжение на внутренней
поверхности
|
|
416
|
1333
|
3,20
|

|
Ф(5,08)=0,9999
|
КРЫШКА
|
Сталь 12X18H9T
|
|
|
|
|
|
Напряжение в средней части крышки
|
|
1213
|
1730
|
1,41
|

|
Ф(1,57)=0,94179
|
ЗАХЛОПКА
|
Сталь 12X18H9T
|
|
|
|
|
|
Максимальное
напряжение в центре захлопки
|
|
1224
|
1730
|
1,41
|

|
Ф(1,57)=0,94179
|
Таблица 2
Параметр
функционирования
|
Среднее значение параметра
yi
|
Ограничения параметра
(yВ, yН)
|
Коэффициент вариации параметра
функционирования
Kyi
(по прил.8)
|

|
Вероятность
безотказной работы
P2j=Ф(ui)
|
Герметичность
в затворе
|
40 см3/мин
|
yВ=120 см3/мин
по ГОСТ
9544-75
|
Кy1=0,27
|
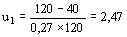
|
Ф(2,47)=0,9932
|
Давление открытия клапана
|
46 см2
по силовому расчету
|
yВ=180 кгс/см2
по ОСТ 26-07-1375-82
|
Кy2=0,15
|
u2
= 19,42
|
Ф(19,4)=0,9999
|
Коэффициент
гидравлического сопротивления
|
1.3
|
yВ=2,7
|
Кy3=0,25
|
u3
= 2,0
|
Ф(2,0)=0,9772
|
Для
проведения расчета заполним таблицу 2.

Вероятность
безотказной работы клапана
обратного составляет

ЗАКЛЮЧЕНИЕ
Вероятность
безотказной работы клапана обратного составляет 0,935.
Расчет
должен быть уточнен испытаниями на надежность и сбором информации об
эксплуатационной надежности.
При
испытаниях контролю подлежат значения параметров функционирования yi, указанные в табл.2.
1.
Разработан ЦКБА ЛНПОА
"Знамя труда" имени И.И. Лепсе. Исполнители: Ю.И. Тарасьев, Г.В.
Котылевский, Т.Г. Потемкина.
2. Утвержден Указанием Минтяжмаша СССР от №
и зарегистрирован за №
3. Срок
первой проверки - 1995 год,
периодичность проверки 5 лет.
4.
Взамен ОСТ 26-07-821-80, ОСТ 26-07-2006-78.
5.
Ссылочные нормативно-технические
документы
Обозначение НТД, на который дана
ссылка
|
Номер пункта, подпункта,
перечисления, приложения, таблицы
|
ГОСТ
27.002-90
|
п.1.1
|
РД 302-07-278-89
|
п.1.6
|
Номер изменения
|
Номер листа (страницы)
|
Номер документа
|
Подпись
|
Дата внесения изменения
|
Дата введения изменения
|
измененного
|
заманенного
|
нового
|
аннулированного
|
|
|
|
|
|
|
|
|
|
|
|